EFFECT OF MAGNETRON SPUTTERING MODES ON THE FORMATION AND COMPOSITION OF TiCN COATINGS
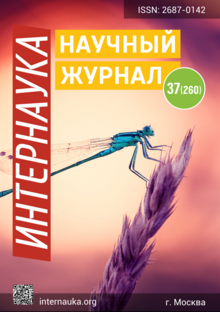
EFFECT OF MAGNETRON SPUTTERING MODES ON THE FORMATION AND COMPOSITION OF TiCN COATINGS
Nauryzbek Bakhytuly
PhD student, Junior Researcher, "Institute of Metallurgy and Ore Beneficiation" JSC at NJSC "Kazakh National Research Technical University named after K.I. Satbayev",
Kazakhstan, Almaty
Axaule Mamaeva
Associate professor, Candidate of Physical and Mathematical sciences, Head of laboratory "Metal science" of the JSC "Institute of Metallurgy and Ore Beneficiation" JSC at NJSC "Kazakh National Research Technical University named after K.I. Satbayev",
Kazakhstan, Almaty
Aidar Kenzhegulov
PhD, Researcher, JSC "Institute of Metallurgy and Ore Beneficiation" JSC at NJSC "Kazakh National Research Technical University named after K.I. Satbayev",
Kazakhstan, Almaty
Aleksandr Panichkin
Candidate of Technical sciences, Head of the National Scientific Collective Use Laboratory of JSC "Institute of Metallurgy and Ore Beneficiation" JSC at NJSC "Kazakh National Research Technical University named after K.I. Satbayev",
Kazakhstan, Almaty
ABSTRACT
Background: The purpose is to evaluate the effect of gas pressure and the gas flow rate, on the formation of TiCN coatings on stainless steel and Ti substrates. Methods: This paper considers the effects of magnetron sputtering modes and composition of gas medium composition on the formation of titanium carbonitride (TiCN) coatings. Result: Such factors as the deposition rate, the plasma flux density on the substrate, the composition and pressure of the reaction gas, have a significant influence on the deposition rate of TiCN films. Conclusion: A change in acetylene content in the reaction gas mixture affects the structural parameters and nanohardness of TiCN coatings. An increase in the C2H2content from 0.324 L/h to 0.470 L/h leads to an increase in nanohardness.
Keywords: magnetron sputtering, titanium carbonitride, protective properties, reaction gas, residual stresses, potential
Introduction. Much information about the physical and mechanical properties of various materials, including the wear resistance of coatings, has been accumulated [1]. The application of wear-resistant coatings is an effective way to improve the performance of cutting tools [2, 3]. A significant increase in nano- and microhardness [4], elastic modulus [5], and, consequently, wear resistance of these materials predetermines the main promising direction of their use – an increase of the durability of products and tools [6]. Wear-resistant coatings are applied to various objects, particularly various parts and assemblies in chemical engineering, and medical and biological objects, which are exposed to simultaneous mechanical and corrosion-enabling chemical factors. Their effective use must be ensured by high corrosion resistance and protective properties of coatings [7].
There are various methods for producing coatings on work surfaces. Considering the specifics of the formation processes of coatings, they can be divided into three main groups. One of them is the method of physical deposition of coatings, usually includes vacuum evaporation, the supply of reaction gas, magnetron sputtering (MS), and electron-beam plasma deposition and others [8]. TiCN coating has satisfactory thermal and wear resistance, and relatively high thermal conductivity compared with coatings based on the carbides and nitrides of other metals that are actively developed and used nowadays [9].
Based on literature review and preliminary experimental studies, it has been found that the main factors affecting the physical and mechanical properties of coatings, determining their functional and performance characteristics, are the reaction gas pressure [10], deposition rate (DR) [11], and coating thickness, as well as the value of the pulse and the constant potential of negative substrate bias [12,13]. They determine the coating structure [14], the size of the crystallites, and the residual internal stresses in them. At critical values, they can cause delamination of the formed layers from the substrate or their cracking [15]. Razmi and Yesildal [16] present an example of the effect of gas flow rate in the MS process on the tribological properties of the obtained coatings. Similarly, Chen et al. [17] confirmed the influence of the choice of the parameters of the sputtering process on the mechanical properties (hardness) and functional properties (wear mechanism) of the obtained coatings. The results of Correa et al. [18] confirm that the tribological properties are strongly dependent on the nature of the coating. However, the deposition parameters have not yet been sufficiently studied and clarified. In this regard, it is of interest to study the effect of these parameters on the structure and properties of TiCN coatings.
Materils and Methods
The deposition of TiCN coatings on substrates, namely, steel AISI 304 and Ti Grade 2, was performed with a MS unit using VT1-0 Ti targets. Further, A5-grade aluminum foil was used to determine the DR and layer thickness. The MS unit is equipped with an APEL-IS-21CELL (Russian Federation) ion source and APELMRE100 unbalanced magnetron (Russian Federation). The sample chamber was evacuated to a base pressure 5-10−3 Pa before deposition. Then, ionic purification of the substrates with argon was performed at an operating voltage of 2.5 kV, a current of 20-25 mA, a pressure of 0.25 Pa, and a duration of 20 min. The MS system’s symmetrical and asymmetrical power supply was used to test the TiCN coating deposition modes. Bias was applied to the substrate with an asymmetric power supply. Potential bias was applied to the substrate using an APEL-M-5PDC (Russian Federation) power supply at a constant bias voltage of 65-120 V. The flows of the inert and reaction gases were controlled using RRG12 flow meters (Russian Federation). The total gas flow rate Ar/C2H2 + N2 was set at a level of up to 2 L/h. The flows of the working gases nitrogen and C2H2 were changed during the deposition of TiCN coatings, which were in the region of 0.08–0.45 L/h and 0.2–0.47 L/h, respectively. The plasma was ignited after reaching the working pressure of Ar/C2H2+N2 gases. Plasma current was fixed in all experiments at 2A. The voltage was automatically varied in the range of 500–800 V. APEL-M-5PDC-1000A-1 (Russian Federation) power supply was used for this purpose. Depending on the task, the deposition time of the coatings was 30 min, 1 h, and 2 h. As determined by scanning electron microscopy (SEM), the TiCN films were about 2.5 mm thick when the deposition time was 2 h.
The surface morphology and thickness of the formed coatings were evaluated by SEM (JXA-8230; Jeol, USA) at an accelerating voltage of 20 kV and an electron-beam current of up to 7 nA. An X-ray diffractometer (D8 Advance Bruker (Germany) ; a-Cu radiation l » 1.54 A; U = 35 kV, I = 20 mA) was used to study the samples by X-ray diffraction analysis (XRD. The Crystallography Open Database was used for the identification of the structures. Nanoindentation was carried out on a nanohardometer “NanoScan-4D”; 10 indentations were made with the help of the Berkovich indenter. Young’s modulus and hardness were determined by the Oliver–Farr method. The DR of pure Ti was determined by the weight method, by weighing the aluminum foil with an area of 36 cm2 before and after sputtering on a Sartorius Cubis MSA3.6P (Germany) microbalance with an accuracy of 1 mg.
Experimental Results and Discussion
Experiments were conducted to determine the effects of (1) argon pressure in the chamber of the MS unit and (2) the voltage of the magnetron solenoid on the DR of Ti film on the surface of an aluminum foil substrate to establish the optimal modes of Ti target sputtering. It was found that the DR decreases from 3.3 mm/h to 2.3 mm/h with increase in the sputtering gas pressure from 0.46 Pa to 0.66 Pa (Figure 1a). The lower DR at a higher argon consumption is apparently associated with a decrease in the titanium concentration in the gas flow, which leads to a smaller fraction of activated particles. With an increase in the consumption of argon, the scattering of the primary electron beam occurs to a greater extent on argon molecules than on titanium. The DR grows from 2.3 mm/h to 2.9 mm/h, as the magnetron solenoid voltage increases from 0 V to 10 V; the DR decreases to 2.24 mm/h, with a further increase in voltage from 10 V to 40 V (Figure 1b). Microprobe analysis of the deposited coatings showed that a stainless steel ring is cosputtered when the voltage on the solenoid is <25 V, thus contaminating the deposited film with iron, nickel, and chromium. Thus, the optimal modes for sputtering a Ti target are pressure in the chamber of 0.46 Pa, which corresponds to an argon flow rate of 1.885 L/h, and a voltage across the magnetron solenoid of 25-30 V.
Figure 1. Effect of argon pressure (a) and magnetron solenoid voltage (b) on the DR of pure titanium at a sputtering current of 2 A
The effect of the flow rate of N2 and C2H2 into the chamber of a MS unit on the DR of TiN and TiC films on an aluminum foil substrate was investigated. It was found that with an increase in the N2 flow from 0.11 L/h to 0.45 L/h, a rapid decrease in the DR from 1.5 mm/h to 1 mm/h is observed; at 0.9 L/h, the DR is 0.9 mm/h (Figure 2a). The supply of Ti atoms gradually decreases as the nitrogen flow rate increases. Since the DR is closely related to the number of Ti atoms reaching the substrate surface, a lower DR means that fewer Ti atoms reach the substrate [19]. An increase in C2H2 flow rate from 0.06 L/h to 0.235 L/h shows a gradual decrease in TiC film DR from 1.7 mm/h to 1.33 mm/h, a further increase in flow rate to 0.35-0.47 L/h sharply reduces the film DR to 0.61-0.63 mm/h (Figure 2b). A loose soot layer is deposited on the surface of the Ti target and the magnetron installation nozzle, which allows us to conclude that at flow rates >0.235 L/h, thermal decomposition of C2H2 in the plasma occurs. The resulting carbon deposited on the surface of the target leads to its contamination and substantially reduces the Ti atomization rate [13]. Impurity elements accumulate at the Ti grain boundary and can prevent the diffusion of atoms [20]. Therefore, the higher the purity of the Ti target, the higher the rate of coating deposition [21]. Thus, we can conclude from the data obtained that when TiCN coatings are deposited, the nitrogen flow rate should not exceed 0.45 L/h, and the C2H2 flow rate should be <0.3 L/h.
The thickness d of the formed coatings (d: ~2.5 mm) was estimated by SEM. The BSE mode was used for all areas of the samples selected for the SEM study, and the results are presented in Figure 3. This figure also shows the morphology of the deposited coating. Analysis of the composition of coatings deposited with an identical flow of the sputtering gas, but at different flow rates of nitrogen and C2H2, showed that there is a decreasing tendency of the Ti content in the coatings with an increase in the carbon concentration in the TiCN films. This observation confirms the conclusions described earlier about the thermal decomposition of C2H2 in the magnetron discharge plasma and the contamination of the Ti target surface with carbon, which reduces the rate of its sputtering.
Comparison of the results from the analyses of the composition of coatings depending on the ratio of sputtering (Ar 1.35 L/h) and reactive gases (at N2/C2H2 ratio = 0.9) suggests that C concentration in the deposited TiCN films increases and Ti and nitrogen contents decrease with increasing reactive gas flow (Figure 4a).
Figure 2. Influence of the N2 (a) and C2H2 (b) flow rates on the DR of the TiN and TiC film at an Ar pressure of 0.66 Pa, a sputtering current of 2 A, and a solenoid voltage of 25 V
Figure 3. SEM images of the morphology (a,b,c) and thickness (c) of the TiCN coating (sputtering current of 2 A, flow rates of sputtering gas and N2+C2H2 of 1.35 L/h and 0.43 L/h, respectively, and a solenoid voltage of 25 V)
The effect of the flow rate of argon on the content of Ti, carbon, and nitrogen in the TiCN film was estimated at a flow rate of 0.08 L/h nitrogen and 0.17 L/h C2H2, and identical sputtering parameters. It was found that the concentration of nitrogen in the deposited films decreases, while carbon and Ti concentrations increase, with an increase in argon flow from 1.35 L/h to 1.885 L/h (Figure 4b).
Figure 4. Effect of the flow rate of the sum of reactive gases with sputtering gas flow of 1.35 L/h (a) and the argon flow rate with N2 = 0.08 L/h and C2H2 = 0.17 L/h (b) on the contents of Ti, carbon, and nitrogen
A change in the content of acetylene C2H2 in the mixture of reaction gases significantly affects the tribological and mechanical properties of TiCN coatings. Figure 5 displays the measured hardness and wear rate (WR) of applied coatings using nanoindentation and tribo testing. Changing the content of acetylene (from 0.21 L/h to 0.47 L/h) leads to a linear increase in nanohardness. This means that the carbon in the respective structure contributes to high hardness in the coatings. Such an increase in nanohardness is manifested in [22]. The WR of the coatings depending on the C2H2 flux shows an unstable character. With an increase in flow from 0.21 L/h to 0.28 L/h, the WR of coatings decreases, a further increase leads to an increase in WR to 1.57 × 10-5 mm3/mN. Such a nonmonotonic change in WR is associated with structural changes in the coating.
Figure 5. Nanohardness diagram of the coatings obtained at acetylene flow rates ranging from 0.324 L/h to 0.470 L/h
Conclusions. The influence of MS parameters and the composition of the gaseous medium on the formation of titanium carbonitride coatings was investigated.
It has been established that the main factors affecting the physical and mechanical properties of nanocrystalline coatings and that consequently determine their functional characteristics include the reaction gas pressure, the deposition rate. TiCN coatings were obtained by MS of a Ti target at the following flow rates: sputtering gas Ar ranging from 1.35 L/h to 1.885 L/h; reactive gases – nitrogen ranging from 0.08 L/h to 0.225 L/h and C2H2 ranging from 0.117 L/h to 0.3 L/h. It was shown that C2H2 causes a decrease in the atomization rate of Ti due to thermal decomposition in the magnetron discharge plasma, which significantly affects the composition of TiCN. A change in the content of C2H2 in a mixture of reaction gases significantly affects the wear rate and nanohardness of TiCN coatings. It was determined that an increase in the C2H2 content from 0.324 L/h to 0.470 L/h leads to an increase in nanohardness. This is associated with structural changes in the coatings.
This research was funded by the Science Committee of the Ministry of Education and Science of the Republic of Kazakhstan (grant number AP08857049).
References:
- Reshetnyak VN, Strelnitsky VE. Synthesis of hardening nanostructured coatings. Quest Atomic Sci Technol. 2008;2:119–30.
- Veprek S, Maritza JG. Veprek-Heijman-industrial applications of superhard nanocomposite coatings. Surf Coat Technol. 2008;202:5063–73.
- Pogrebnyak AD, Shpak AP, Azarenkov NA, Beresnev VM. Structure and properties of hard and superhard nanocomposite coatings. UFN. 2009;179(1):35–64.
- Rakhadilov B, Kozhanova R, Popova N, Nugumanova A, Kassymov A. Structural-phase transformations in 0.34C–1CRr–1Ni–1Mo–Fe steel during plasma electrolytic hardening. Mater Sci Pol. 2020;38(4):699–706.
- Riester L, Bell TJ, Fischer-Cripps AC. Analysis of depth-sensing indentation tests with a Knoop indenter. J Mater Res. 2001;16(6):1660–65.
- Pogrebnyak AD, Drobyshevskaya AA, Ilyashenko MV, Kirik GV, Komarov FF, Beresnev VM, Makhmudov NA, Ruzimov ShM, Shipilenko AP, Tuleushev JZ. Tribotechnical, physical, and mechanical properties and thermal stability of nano and microcomposite coatings based on Ti-Al-N. Phys Eng Surf. 2010;8(1):20–7.
- Pogrebnjak AD, Kravchenkoa YuA, Kislitsynb SB, Ruzimovc ShM, Nolid F, Misaelidesd P, et al.. TiN/Cr/Al2O3 and TiN/Al2O3 hybrid coatings, structure features and properties resulting from combined treatment. Surf Coat Technol. 2006;201:2621–32.
- Tabakov VP. Rabotosposobnost’ režuŝego instrumenta s iznoso- stojkimi pokrytiâmi na osnove složnyh nitridovi karbonitridov titana. Ulʹânovsk: UlGTU; 1998. [in Russian].
- Kenzhegulov A, Mamaeva A, Panichkin AV, Prosolov KA, Brończyk A, Capanidis D. Investigation of the adhesion properties of calcium-phosphate coating to titanium substrate with regards to the parameters of high-frequency magnetron sputtering. Acta Bioeng Biomech. 2020;22(2):111–120.
- Blinkov IV, Volkhonsky AO, Anikin VN, Konyukhov YuV. Nanostructured wear-resistant coatings based on multicomponent nitrides obtained by vacuum-arc ion-plasma deposition. Phys Chem Surf Prot Mater. 2012;48(6):546–53.
- Panda A, Dyadyura K, Hovorun T, Pylypenko O, Dunaeva M, Pandova I. Nanostructured wear-resistant coatings based on refractory metals nitrides: physical-mechanical properties and structural-phase state. Manage Prod Eng Rev. 2019;4(10):133–9.
- Saoula N, Madaoui N, Tadjine R, Erasmus RM, Shrivastava S, Comins JD. Influence of substrate bias on the structure and properties of TiCN films deposited by radio-frequency magnetron sputtering. Thin Solid Films. 2016;616:521–529.
- Akkaya SS, Vasyliev VV, Reshetnyak EN, Kaz-manlı K, Solak N, Strel’nitskij VE, Ürgen M. Structure and properties of TiN coatings produced with PIII&D technique using high efficiency rectilinear filter cathodic arc plasma. Surf Coat Technol. 2013;236:332–40.
- Mamaeva AA, Kenzhegulov AK, Panichkin AV, Alibekov ZhZh, Wieleba WK. Effect of Magnetron Sputtering Deposition Conditions on the Mechanical and Tribological Properties of Wear-Resistant Titanium Carbonitride Coatings. Coatings 2022;12(2):193. https://doi.org/10.3390/coatings12020193
- Zheng XH, Tu JP, Gu B, Hu SB. Preparation and tribological behavior of TiN/a-C composite films deposited by DC magnetron sputtering. Wear. 2008;26:261–5. https://doi.org/10.1016/j.wear.2007.10.007.
- Polcar TR, Novak P, Siroky P. The tribological characteristics of TiCN coating at elevated temperatures. Wear. 2006;260:40–9. https://doi.org/10.1016/j.wear.2004.12.031.
- Razmi A, Yesildal R. Microstructure and mechanical properties of TiN/TiCN/TiC multilayer thin films deposited by magnetron sputtering. Preprints 2018, 2018070127. https://doi.org/10.20944/preprints201807.0127.v1.
- Chen R, Tu JP, Liu DG, Mai YJ, Gu CD. Microstructure, mechanical and tribological properties of TiCN nanocomposite films deposited by DC magnetron sputtering. Surf Coat Technol. 2011;205:5228–34. https://doi.org/10.1016/j.surfcoat.2011.05.034.
- Correa JF, Aperador W, Caicedo JC, Alba NC, Amaya C. Structural, mechanical and tribological behavior of TiCN, CrAlN and BCN coatings in lubricated and nonlubricated environments in manufactured devices. Mater Chem Phys. 2020;252:123164. https://doi.org/10.1016/j.matchemphys.2020.123164.
- Huang, J.-H., Lau, K.-W., & Yu, G.-P. (2005). Effect of nitrogen flow rate on structure and properties of nanocrystalline TiN thin films produced by unbalanced magnetron sputtering. Surface and Coatings Technology, 191(1), 17–24. doi:10.1016/j.surfcoat.2004.07.066
- Yang, W.-H.; Tang, B.; Bao, M.-D.; Chang, Y.-Q.; Wang, Y.-P.; Zhao, G.-H.; Zhang, L.-J. Surface Morphology and Sputtering Mechanism of Etched Areas of a Metallic Target by Magnetron Sputtering. J. Electron. Mater. 2021, 50, 2409–2416. [CrossRef]
- Liu, L.; Li, W.; Sun, H.; Wang, G. Effects of Ti Target Purity and Microstructure on Deposition Rate, Microstructure and Properties of Ti Films. Materials 2022, 15, 2661. https://doi.org/10.3390/ma15072661
- Tillmann W., Momeni S. Tribological development of TiCN coatings by adjusting the flowing rate of reactive gases // Journal of Physics and Chemistry of Solids. – 2016. – Т. 90. – С. 45-53.