SEPARATION OF Nd FROM MIXTURE CHLORIDE SOLUTION WITH Pr BY SOLVENT EXTRACTON WITH 70% SAPONIFIED PC88A: MIXER-SETTLER EXPERIMENTS
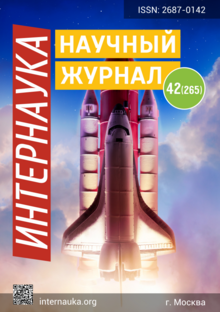
SEPARATION OF Nd FROM MIXTURE CHLORIDE SOLUTION WITH Pr BY SOLVENT EXTRACTON WITH 70% SAPONIFIED PC88A: MIXER-SETTLER EXPERIMENTS
Nguyen Van Tung
M.S., Institute for Technology of Radioactive and Rare elements,
Vietnam, Ha Noi
Nguyen Dinh Viet
M.S., Institute for Technology of Radioactive and Rare elements,
Vietnam, Ha Noi
Ngo Quang Huy
M.S., Institute for Technology of Radioactive and Rare elements,
Vietnam, Ha Noi
Nguyen Thi Lien
M.S., Institute for Technology of Radioactive and Rare elements,
Vietnam, Ha Noi
Luu Xuan Dinh
Ph.D, Institute for Technology of Radioactive and Rare elements,
Vietnam, Ha Noi
Acknowledgments:
This research was financially supported by the Ministry project of VINATOM (code DTCB.07/21/VCNXH)
ABSTRACT
Solvent extraction of Pr and Nd from chloride solution was carried out using 70% saponified PC 88A for separation of high purity Nd. A box-type 120 stages mixer-settler system was used including 100 stages of extracted separation and scrubing; and 20 stages of tripping. The extraction process bases on the distribution coefficients of Nd were higher than those of Pr and other reasonable conditions. Results indicated that the balance of extraction process is obtained in 80 hours and product of neodymium more than 99 % purity was obtained.
Keywords: Solvent extraction, Nd, PC88A, separation ….
Introduction
Neodymium (Nd) is one of the most abundant elements of rare earths and is used in high energy product, high coercive force magnets for computers and other applications [1-4]. Nd is obtained from the processing of rare earth ores, then extracted and refined to obtain high purity Nd [5-6]. The separation of Nd from other rare earth fractions, especially its neighbor element praseodymium (Pr), is difficult [7,8].
Solvent extraction is one of the most important methods to separate and purify REEs because of higher purified yield, simple operation compared to classic methods and higher yield and achievement of huge production compared to ion exchanging method.
Among the organophosphorus extraction solvents, PC88A is the solvent with the highest separation coefficient [9-11]. PC88A is phosphorus acidic solvent, so in order to extract REs metal ions, the solvent PC88A firstly needs to be neutralized by alkali aqueous solution or ammonium aqueous solution. The advantages of PC88A solvent are stable and high separated coefficient. The main reactions occurring in RE extraction by PC88A as bellow:
- Neutralized and extraction reaction:
3[HP] + 3NaOH + LnCl3 = LnP3 + 3NaCl + 3H2O (1)
- Reaction for stripping process:
LnP3 + 3HCl = 3[HP] + LnCl3 (2)
Comparing the results obtained up to the present level of investigations, it can be observed that maximum separation factor between Pr and Nd is very low (1.5) [12-17]. Thakur et al. [18] developed an extraction and scrubbing process for the recovery of pure Nd (>96% Nd2O3) from mixture of all lighter rare earths using 20% saponified PC 88A and pure Nd solution as a scrub feed. The authors [18] clearly described that the separation factor between Pr and Nd is around 1.64 which is higher than that of D2EHPA reported by Pierce and Peck [19]. Nevertheless, the results reported eventually suggested that a large number of stages in a mixer–settler operation are required for the separation of Nd and Pr [20].
In the present study, solvent extraction of Pr and Nd from chloride solution was carried out using 70% saponified PC 88A for separation of high purity Nd. For this purpose, a box-type 120 stages mixer-settler system was used. REE solvent extraction flowsheets usually consist of a saponification section, an extraction section, a scrub section, and a strip section. Saponification is a pre-treatment step for pH control during extraction. The extraction section provides bulk separation of the desired REE from the aqueous phase. The spent aqueous phase exits the extraction section as the raffinate. Loaded organic solvent enters the scrub section, where undesirable REE that were co-extracted in the extraction section are scrubbed from the loaded organic phase. Scrubbing is accomplished by contacting the loaded organic phase with an aqueous solution that alters the acid or REE equilibrium conditions. Undesired REE species are transferred to the aqueous phase, which is typically recombined with the extraction aqueous feed to recover any desired REE that were unintentionally scrubbed out of the loaded organic phase. Finally, the scrubbed loaded organic enters the strip section, where the REE is recovered from the organic phase as a rich liquor (RL) product. The organic phase, now stripped of any solutes, is recycled for reuse.
Experimental
Materials
2-Ethylhexylphosphonic acid mono-2-ethylhexyl ester (PC 88A) was purchased from Japan, and used as such without any further purification. The sodium salt of PC 88A (70% neutralized) was prepared by adding stoichiometric amount of concentrated NaOH solution and stirring the mixture until a single phase was formed. IP2028 purchased from Japan was used as dilution because of high capacity in dissolving PC88A, insolubility in water, high stability and less evaporability.
The mixed solution of Pr and Nd chloride obtained from the process of dividing groups of rare earth elements from total Ben Den rare earth oxides was used as the feed solution. The composition of the feed solution is shown in Table 1.
Table 1.
Component of RE in feed solution for separating Nd and Pr
Elements |
Unit |
Feed solution |
Sc |
mg/L |
0.08 |
Y |
mg/L |
0.27 |
La |
mg/L |
0.25 |
Ce |
mg/L |
0.05 |
Pr |
mg/L |
20717.77 |
Nd |
mg/L |
79282.31 |
Sm |
mg/L |
0.18 |
Eu |
mg/L |
0.05 |
Gd |
mg/L |
0.08 |
Tb |
mg/L |
0.09 |
Dy |
mg/L |
0.05 |
Ho |
mg/L |
0.05 |
Er |
mg/L |
0.07 |
Tm |
mg/L |
0.12 |
Yb |
mg/L |
0.17 |
Lu |
mg/L |
0.01 |
TREEs |
mg/L |
100001.60 |
Other chemicals as HCl, NaOH was purchased from Thailand.
Equipments
The pilot-scale extraction system consists of:
- 120 box mixer-settle type-box extraction systems, the volume of each box are 20L, in which 100 boxes for extraction, scrubbing and 20 boxes for stripping.
- Mixer-settle tank to neutralize solvent solution
- Operation chamber.
- Pump system to pump solution using piston and accurate flow meters.
- pH meters
- Purified water filtering system.
- Ventilation system to remove dust and gases.
Figure 1. The diagram of mixer-settler extraction system
Figure 2. Box-type 120 stages mixer-settler system
Methods
The concentration of metals in the aqueous phase, before and after distribution, was measured spectrophotometrically (ICP–OES) (Ultima 2- Horiba- Japan) and atomic absorption spectrum (AAS) (Perkiln Elmer-US).
Results and Discussion
Prepare the solvent extraction system
The feed solution was loaded into the first 100 stages of the extraction system at 1/2 the volume of each stage. 5N HCl was loaded into the remaining 20 stages of the tripping zone at 1/2 volume each. Solvent was loaded into the entire extraction system from order 1 to 120.
The PC88A 20% is neutralized by 4.5N NaOH solution at neutralization tank. The reactions occurring in RE extraction by PC88A as equation (1) and, which is led into boxes in extraction system. pH value of neutralization tank is controlled in the range from 3 to 5.
The TREEs of extraction stages is 80 (from box 1 to box 80) with content of feed in Table 1. The TREEs of scrubbing and tripping stages is 40 (from box 81 to box 120) by 5N HCl solution.
The checking point in which density value is controlled carefully is box 77. The density values at box 1 and box 77 and other parameters of system are checked for every 2 hour. The density values of box 1, 10, 20, 30, 40, 50, 60, 70, 77 and 80 are checked one time every day and the density results are showed on a graph. The concentrations (mg/L) of Pr and Nd are analyzed one time everyday by using ICP-MS device.
Based on obtained results, trend of process was considered to choose the number of box in which new feed is added and the number of box in which the process product is taken out.
Balanced running process
Operation solvent extraction with parameter below:
- Solvent PC88A 20%, with flow rate 2 L/min
- 4.5N NaOH with flow rate 0.09 L/min
- pH value in neutralization 2.8- 3.2
- 5N HCl with flow rate 0.22 L/min (Turning point at box 77, density 1.15).
- Concentrate of RE feed is 150 g/L
- Rafinate added in neutralization tank so that pH value range from 2.8 to 3.2
After operated 80 hrs, the density values of box 1, 10, 20, 30, 40, 50, 60, 70, 77 and 80 are not change. This showed that solvent extraction system had been balance. The results of analysis of Pr and Nd concentrations in the boxes after 80 hrs of operation are shown in Table 2 and Figure 3.
Table 2.
Pr and Nd concentrations in different boxes after 80 hours of operation
Box number |
Pr |
Nd |
Total (mg/l) |
1 |
125034.7 |
708.7 |
125743.4 |
10 |
146398.6 |
6762.3 |
153160.9 |
20 |
110524.3 |
41188.5 |
151712.8 |
30 |
36240.4 |
120491.8 |
156732.2 |
40 |
15357.1 |
143545.1 |
158902.2 |
50 |
9628.4 |
149077.9 |
158706.3 |
60 |
4408.1 |
150307.4 |
154715.5 |
70 |
1629.4 |
150102.5 |
151731.9 |
80 |
422.5 |
149795.1 |
150217.6 |
90 |
130.8 |
147643.4 |
147774.2 |
100 |
37.2 |
811.7 |
848.9 |
Figure 3. Distribution of Pr and Nd in extraction boxes after 80 hours of operation
The results presented in Figure 3 showed that, during the extraction process, the concentration of Pr gradually decreased from box 1 to box 100, whereas the concentration of Nd gradually increased; Pr and Nd were distinctly separated after 80 hours of operation.
The data in Table 2 showed that the trend in the last stages, the larger the number of stages, the higher the concentration of Nd; at box 90, the concentration of Nd is 147 g/L and Pr is 0.13 g/L, meaning that the purity of Nd has reached over 99%. This is because in a mixture of Pr and Nd, Nd has the ability to extract in the zone of high acidity, so Nd will go towards the tripping zone and Pr will go to the extraction zone.
After the extraction system reaches balance, the feed solution is added and the product is removed.
Feeding and taking products process
Determining the order box to remove the Nd product from the extraction system should take into account factors related to the efficiency and material balance of the system. At the high order numbers at the end of system (about box 100) with high Nd content can be selected to remove Nd from the system. However, at the box 100, there is a high acid content, so if the product is collected, the amount of acid according to the product remove together, causing the acid imbalance of the system, causing the concentration of acid supplied to the first box of the extraction system to decrease and the Pr and Nd division would require the addition of acid. Therefore, the optimal point chosen to get the product Nd is of box 90 and Pr is taken at box 2.
The feed solution was loaded into box 35 with a flow rate of 150 ml/min and a TREEs concentration of 100 g/L, Pr concentration of 20.72% and Nd concentration of 79.28%.
From Table 2, we have Nd product removed from box 90 with RE concentration of 147.77 g/L. Let B be the product flow Nd, so:
(3)
Product Pr is removed from box 2 with the concentration of RE calculated as follows: RE concentration in box 2 is 130.9 g/L. Let C is the flow of product Pr removed:
(4)
The results shown in Table 3 and Figure 4 showed that the process of feeding in and taking out the NdCl3 product still maintains the balance of the extraction system. The Nd product obtained was over 99% purity (Table 4). A diagram for extraction process of Pr and Nd from chloride solution by 70% saponified PC 88A for separation of high purity Nd has been proposed (Figure 5).
Table 3.
Pr and Nd concentrations in different boxes during taking products process
Box number |
Pr |
Nd |
Total (mg/l) |
1 |
127102.1 |
701.2 |
127803.3 |
10 |
147212.4 |
6547.2 |
153759.6 |
20 |
109632.1 |
42176.5 |
151808.6 |
30 |
35428.4 |
121552.4 |
156980.8 |
40 |
15057.8 |
145217.0 |
160274.8 |
50 |
9428.5 |
152721.7 |
162150.2 |
60 |
4273.9 |
152105.2 |
156379.1 |
70 |
1552.1 |
152008.2 |
153560.3 |
80 |
417.4 |
150205.6 |
150623.0 |
90 |
128.5 |
148201.3 |
148329.8 |
100 |
37.1 |
815.2 |
852.3 |
Figure 4. Distribution of Pr and Nd in extraction boxes during taking products process
Table 4.
Component of REEs in Nd and Pr product
Elements |
Unit |
Nd product |
Pr product |
Sc |
mg/L |
0.02 |
0.03 |
Y |
mg/L |
0.18 |
0.23 |
La |
mg/L |
0.14 |
0.26 |
Ce |
mg/L |
0.03 |
0.04 |
Pr |
mg/L |
129.42 |
130607.21 |
Nd |
mg/L |
147782.15 |
701.14 |
Sm |
mg/L |
0.13 |
0.11 |
Eu |
mg/L |
0.03 |
0.02 |
Gd |
mg/L |
0.05 |
0.03 |
Tb |
mg/L |
0.07 |
0.04 |
Dy |
mg/L |
0.03 |
0.03 |
Ho |
mg/L |
0.04 |
0.03 |
Er |
mg/L |
0.05 |
0.02 |
Tm |
mg/L |
0.09 |
0.05 |
Yb |
mg/L |
0.09 |
0.06 |
Lu |
mg/L |
0.01 |
0.01 |
Figure 5. Diagram for individual separation Pr and Nd from chloride solution by 70% saponified PC88A
Conclusions
The extraction process of Pr and Nd from chloride solution by 70% saponified PC88A for separation of high purity Nd was studied on pilot scale using a box-type 120 stages mixer-settler system was used including 100 stages of extracted separation and scrubing; and 20 stages of tripping. With solvent extraction parameters: solvent feeding rate 2L/min, feed rate (100 g/L) is 150 mL/min with 0.09 L/min 4.5 N NaOH and 0.22 L/min 5N HCl, pH controled at 2.8-3.2, balance time is 80 hrs. Feed solution was loaded at box 35, Nd product was taken at box 90 with flow of 80 mL/min and purity over 99%. A diagram for extraction process of Pr and Nd from chloride solution by 70% saponified PC 88A for separation of high purity Nd has been proposed.
References:
- Alonso E., Sherman A. M., Wallington T. J., Everson M. P., Field F. R., Roth R., Kirchain R. E. “Evaluating rare earth element availability: a case with revolutionary demand from clean technologies” Environ. Sci. Technol., 46, 3406-3414 (2012).
- Brown, D., Ma, B.M., Chen, Z., 2002. “Developments in the processing and properties of NdFeb-type permanent magnets”. Journal of Magnetism and Magnetic Materials 248, 432–440.
- Liu, G., Chen, X., 2007. “Spectroscopic properties of lanthanides in nanomaterials”. In: Gschneidner, K.A., Bünzli, Jr., J. C.G., Pecharsky, V.K. (Eds.), Handbook on the Physics and Chemistry of Rare Earths, vol 37, pp. 99–169
- Doyle, F.M., Benz, M.G., Shei, J.C., Bao, D.S., Ku, H.X., Zhen, N.D., 2000. “Direct production of mixed, rare earth oxide feed for high energy-product magnets”. In: Bautista, R.G., Mishra, B. (Eds.), Rare Earths and Actinides: Science, Technology and Applications IV. TMS, Warrendale, PA, pp. 31–44.
- J. B. Hedrick. “Mineral Commodity Summarie, January” U. S. Geological Survey, 132-133 (2004).
- Baba Y., Kubota F., Kamiya N., Goto M. “Selective recovery of dysprosium and neodymium ions by a supported liquid membrane based on ionic liquids” Solvent. Extract. Res. Dev., 18, 193-198 (2011b).
- C.K. Gupta, N. Krishnamurthy, Extractive Metallurgy of Rare Earths, CRC press, New York, NY, 2004.
- Feng Xie, Ting An Zhang, David Dreisinger, Fiona Doyle, “A critical review on solvent extraction of rare earths from aqueous solutions”, Minerals Engineering 56 (2014) 10–28
- Preston J. S. “Solvent extraction of the trivalent lanthanides and yttrium by some 2-bromoalkanoic acids” Solvent Extraction and Ion Exchange, 12(1), 29-54 (1994).
- Zhang, Y., Li, J., Huang, X., Wang, C., Long, Z., Zhu, Z., Zhang, G., 2007. “Synergistic extraction of rare earths by mixtures of di(2-ethylhexyl)phosphoric acid and (HDEHP) and 2-ethylhexyl phosphoric acid mono-2-ethylhexyl ester (HEH/EHP) in sulfuric acid media”. Journal of The Chinese Rare Earth Society 26 (6), 671–676 (in Chinese).
- Preston, J.S., du Preez, A.C., 1995. “Solvent extraction of neodymium (III) and erbium (III) bv mixtures of 3,5-diisopropylsalicylic acid and neutral organophosphorous compounds”. Solvent Extraction and Ion Exchange 13 (1), 27–41.
- Itoh M., Miura K., Machida K.I., “Extraction of rare earth elements from Nd-Fe-B magnet scraps by NH4Cl” Chem. Lett., 37, 372-373 (2008)
- Itoh M., Miura K., Machida K. “Novel rare earth recovery process on NdFeB magnet scrap by selective chlorination using NH4Cl” Journal Alloys Compd., 477, 484-487 (2009).
- Ying, X., Wang, X., Li, D., 2005. “Synergistic extraction and separation of heavy lanthanide by mixtures of bis(2,4,4-trimethylpentyl)phosphinic acid and 2-ethylhexyl phosphinic acid mono-2-ethylhexyl ester”. Separation Science and Technology 40 (11), 2325–2336.
- Wang, X., Li, W., Meng, S., Li, D., 2006. “The extraction of rare earths using mixtures of acidic phosphorus based reagents or their thio-analogues”. Journal of Chemical Technology and Biotechnology 81, 761–766..
- K. Lyon, M. Greenhalgh, R. S. Herbst, T. Garn, A. Welty, M. D. Soderstrom, B. Jakovljevic, “ENHANCED SEPARATION OF RARE EARTH ELEMENTS”, 2016 International Mineral Processing Congress.
- Gupta, C.K., & Krishnamurthy, N. (2005). “Extractive Metallurgy of Rare Earths”. Washington, DC: CRC Press.
- Raju Banda, Ho Seok Jeon, Man Seung Lee, “Separation of Nd from mixed chloride solutions with Pr by extraction with saponified PC 88A and scrubbing”, J. Ind. Eng. Chem. (2014)
- Jia, Q., Tong, S., Li, Z., Zhou, W., Li, H., Meng, S., 2009. “Solvent extraction of rare earth elements with mixtures of sec-octylphenoxy acetic acid and bis(2,4,4- trimethylpentyl) dithiophosphinic acid”. Separation and Purification, Technology 64, 345–350.
- Nair, S.G.K., Smutz, M., 1967. “Recovery of lanthanum from didymium chloride with di(2-ethylhexyl) phosphoric acids solvent”. Journal of Inorganic and Nuclear Chemistry 29, 1787–1797.