MELTING CAST IRON FROM NIX GRAIN WASTE AND APPLICATION IN COPPER CEMENTATION PROCESS
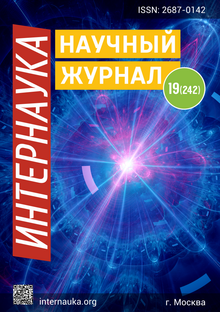
MELTING CAST IRON FROM NIX GRAIN WASTE AND APPLICATION IN COPPER CEMENTATION PROCESS
Nguyen Ba Phuong
M.S., Institute of Materials Science – Vietnam Academy of Science and Technology,
Vietnam, Hanoi
Nguyen Trung Kiên
M.S., Institute of Materials Science – Vietnam Academy of Science and Technology,
Vietnam, Hanoi
Pham Duc Thang
Assoc. Prof., Ph.D, Institute of Materials Science – Vietnam Academy of Science and Technology,
Vietnam, Hanoi
Ngo Huy Khoa
PhD., Institute of Materials Science – Vietnam Academy of Science and Technology,
Vietnam, Hanoi
Do Nguyen Huy Tuan
M.S., Institute of Materials Science – Vietnam Academy of Science and Technology,
Vietnam, Hanoi
Do Thi Duyen
M.S., Institute of Materials Science – Vietnam Academy of Science and Technology,
Vietnam, Hanoi
Le Hong Duyen
M.S., Institute of Materials Science – Vietnam Academy of Science and Technology,
Vietnam, Hanoi
Nguyen Thi Hong Nhung
M.S., Sao Do University - Ministry of Industry and Trad,
Vietnam, HaiDuong
ABSTRACT
Currently, the metallurgical industry faces a number of challenges such as the rapid depletion of metal mines, energy costs or increasing environmental concerns. Copper slag or nix grain waste is one of the hazardous wastes that are receiving the attention of the government as well as scientists in many countries because it not only pollutes the environment but also causes loss of many precious metals. The technology of recycling nix grain waste by melting in electric arc furnace is presented in this paper. The mechanical properties of cast iron were also studied and evaluated. The result showed that cast iron has mechanical properties equivalent to civil cast iron products. Especially, cast iron after melting is applied in copper cementation process to recover copper in copper-containing solutions with efficiency of 94.35%.
Keyword: Nix grain waste, cast iron, electric arc furnace, cementation process.
1. Introduction
In the maritime industry, cargo ships which have the tonnage from 10.000 to 150.000 tons are regularly maintained and repaired to ensure safety. Nix grain waste or copper slag are used to rust removing for the ships by metal grinding method [1]. The impact of the abrasive grain on the machined surface creates a concentrated force large enough to cause a small crack, and then the gas flow carries both the abrasive grain and the piece of cracked material away. This method is very convenient for machining brittle and fragile materials. In addition, it is also used to remove the oxide layer and thin films of impurities on the surface of the hull; clean the surface details; cut small holes, grooves, or complex patterns on hard or brittle metal materials or non-metallic materials...This method has the advantages such as fast construction, low cost, high efficiency. However, when using this technology, it will emit pollutants into the environment, which can cause heavy metal poisoning, serious neurological and respiratory diseases [2]. The reason is that the dust component which discharged during cleaning of the hull contains dust of nix grain waste, dust caused by peeling paint and dust caused by metal rust. In this mixture, there are many impurities, toxic heavy metals, which adversely affect the environment by exceeding the permissible level. On the other hand, the management of the nix grain waste dump is only temporary. That is to build a wall around it and use asbestos-cement shingle to cover it. However, when using this method, a large amount of nix grain waste will follow the flow to seep into the soil when it rains. This will affect the soil and water environment and cause poisoning. Therefore, if we do not handle in time, nix grain waste will affect the health of people as well as the environment around the plant area [2].
Furthermore, the price of iron ore tends to increase rapidly in recent years. This is due to the scarcity input materials as well as the increasing demand for iron ore in the industry. Therefore, finding materials to replace iron ore in steelmaking becomes urgent [3]. One of the solutions is to melt cast iron from nix grain waste.
Additionally, cast iron that melted from nix grain waste is also used in the copper cementation process. Currently, there are several methods to recover copper and one of them is cementation. This is a method of creating an electrochemical precipitation of a metal from its salt solution. Actually, the cementation process is applied in using zinc dust to precipitate gold and silver from cyanide solutions or using iron to recover copper from copper containing solutions. The precipitation of copper on iron from its salt solutions uses a chemical reaction, specifically [4]:
CuSO4 + Fe → Cu + FeSO4
(aq) (s) (s) (aq)
Moreover, cast iron melted from nix grain waste or copper slag has the high copper content, so we can recover both copper powder in a copper-containing solution and the amount of copper in cast iron. Especially, cast iron melted from nix grain waste or copper slag is cheaper than iron powder. This will increase the economic efficiency of the copper hydrometallurgical process.
2. Experimental procedure
The cast iron pattern was melted from nix grain waste with the selected slag: SiO2 – Al2O3 – CaO (SiO2: 49%, Al2O3: 15% and CaO: 36%). In addition, the fluxes were used in the melting process such as lime, coal, and quartzite. The ratio of mixed materials for the melting process of 10 kg of nix grain was as follows: coal: 1.52 kg, lime (CaO): 2.17 kg and Al2O3: 0.286 kg
Firstly, grind the above mixture in the ball mill to obtain a grain size from 3 to 7 mm. Secondly, it is baked in a mold that has size 100x50x50 mm. After that add bait slag and adjust the current in the electric arc furnace to about 1200A to melt the slag layer. When the slag layer has melted, we proceed to provide mixed material in the furnace. Divide them into several parts about 2kg per portion and about 30 minutes apart each time. After adding mixed material, we adjust the current in the furnace to about 800A, the current is stabilized so that the electrode is flooded with a mixture of metal and liquid slag. Finally, conduct 800A current for a period of 30 minutes after the last providing. The melting time is about 2 hours and the melting temperature >1400oC to ensure that the cast iron and slag are melted. Cast iron melting experiments were carried out on an electric arc furnace with a capacity of 15 KVA at the Institute of Materials Science (IMS). The cast iron pattern was measured for mechanical properties and analyzed by scanning electron microscope method (SEM)..
The cast iron pattern after the melting process was put into a copper sulfate solution to evaluate the ability to recover copper by the cementation process. First of all, add 10l of copper sulfate solution with concentration of 15g/l and pH=1.3 into a container with a stirring system. After that slowly add granular cast iron into the container. The stirring speed which used in this experiment was 100 rpm and the size of the granular cast iron was about 0.8 - 0.9 cm in diameter. After the time points, the copper powder was recovered and then washed with water, dried, and evaluated the copper recovery efficiency when using granular cast iron.
3. Results and discussion
In cast iron melting process, SiO2 and Al2O3 play an important role in determining the properties of furnace slag because these are two acidic oxides [5]. In addition, the main components of the flux are CaO and MgO, which are two alkaline oxides [6]. In fact, their melting temperatures are very high: Tmelt (SiO2) = 1713oC, Tmelt (Al2O3) = 2050oC, Tmelt (CaO) = 2570oC and Tmelt (MgO) = 2880oC [7]. Therefore, these compounds are not melted during the melting process, but only have a mutual effects.
In addition, temperature also affects the viscosity of the slag [8]. The viscosity of alkaline slag (CaO, Na2O, K2O,...) is usually lower than that of acid slag (SiO2, P2O5, Cr2O3,...) [9]. However, if the acid slag is added with alkaline oxides, the viscosity will decrease sharply and vice versa. In the melting process, the slag often has a high viscosity because the nix grain waste have a high SiO2 content [10]. Therefore, the most commonly used flux is lime (CaO) to reduce the acidity, increase the dilution of the slag and ensure a favorable melting process.
Table 1.
Chemical compositions of melting slag
Element |
Content (%) |
Fe |
13.18 |
C |
12.67 |
O |
39.15 |
Al |
4.97 |
Si |
18.09 |
S |
0.43 |
Cu |
0.29 |
Na |
0.66 |
K |
0.75 |
Mg |
1.88 |
Ca |
7.39 |
Ti |
0.27 |
Cr |
0.02 |
Mn |
0.25 |
Total |
100.00 |
Table 2.
Chemical compositions of cast iron
Element |
Content (%) |
Fe |
89.18 |
C |
3.26 |
O |
2.35 |
Al |
0.05 |
Si |
2.09 |
S |
0.54 |
Cu |
2.01 |
Cr |
0.52 |
Total |
100.00 |
From Table 2, it shows that the content of C is 3.26% and Cu is 2.01% in cast iron, so the process of melting cast iron pattern from nix grain waste has achieved the desired results [10]. The amount of iron and copper is lost to the slag and partly to vaporization due to environmental conditions in the furnace. From Table 1, it shows that the content of heavy metals (Mg, Ti, Cr, Mn...) is very low in the slag (mostly less than 1%). Therefore, the slag from this melting process can be safely discharged into the environment [11]. However, the cast iron product still has high sulfur content, so the research and development of technology to reduce the sulfur content and improve the product quality of cast iron needs to be continued to be tested in the next studies.
|
|
(a) |
(b) |
Figure 1. Microstructure of the cast iron pattern (a) and slag pattern (b) |
The cast iron pattern has a biphasic structure with a mixture of graphite - ferritic phases as observed in Figure 1. In the cast iron pattern, graphite has a flat plate shape in three-dimensional space and the plate graphites are on a ferritic substrate. If it viewed in two-dimensional space, such as observing a polished surface, the graphite fragments appear as thin fibers. The firsts part of the graphite flat plate plays as the pre-existing notches; stress will concentrate at those points and create brittleness for the material [12,13]. The presence of those graphite crystals gives cast iron its machinability properties due to its tendency to fracture along the graphite crystals. In addition, the cast iron has a very good ability to absorb forces (damper), so it is often used as the base for machinery and equipment.
In the process of melting nix grain waste, slag is created which includes the main elements: Fe, C, O, Ca and S. The slag has amorphous structure, rough surface the voids and angles that are shown in figure 1. Because of this property, slag is often used as the borrow material. In addition, the volumetric mass of the slag is in the range (2.40 – 2.50) g/cm3, lower than that of natural limestone and larger than that of blast furnace slag. Slag is also often used as an aggregate for concrete and in construction with a water absorption of about 1.0 to 6.0 %. Moreover, the abrasion and shock resistance of slag aggregates is also higher than that of natural aggregates.
Table 3.
Tensile test results of cast iron pattern melted from nix grain waste
Parameter |
Content (%) |
So: Pattern cross-section (cm2) |
10.68 |
Lo(lt): Theoretical length of pattern (cm) |
11.05 |
L1: Length of pattern after tensile test (cm) |
11.63 |
A: Elongation (%) |
36.05 |
Fch: Traction (N/mm2) |
20000 |
|
306.62 |
|
338.22 |
The results of mechanical analysis of the cast iron pattern after melting are shown in Table 3. Due to the influence of graphite in the form of plates, cast iron has much worse mechanical properties than steel [10,14]. Especially, graphite has a low strength, so it looks like voids and cracks that lose the continuity of the metal base in the cast iron, thereby drastically reducing the tensile strength [15].
The mechanical properties of cast iron also depend on the quantity and distribution of graphite [10]. The more graphite, the more voids, the worse the mechanical properties of cast iron. In particular, the size of graphite also affects the mechanical properties of cast iron pattern. The longer the plate graphite (the larger the metal-based separation), the lower the mechanical properties of cast iron [10]. In order to improve the mechanical properties of cast iron, it is necessary to use measures to smooth and small the graphite so that the shorter, smaller, and more curved the graphite, the better.
Table 4.
Effect of cementation time on copper recovery efficiency
Time (minutes) |
Copper recovery efficiency (%) |
3 |
31.26 |
5 |
64.73 |
10 |
80.64 |
15 |
90.12 |
20 |
93.76 |
25 |
94.35 |
Table 4 shows the influence of cementation time on copper recovery efficiency of copper sulphate solution when using melted cast iron from nix grain waste. According to Table 1, cast iron has 89.18% iron, so the cementation process will take place in copper sulfate solution. In addition, the cast iron pattern contains high sulfur content (0.54%) so the cast iron will be porous [14]. This also favorably facilitates the cementation process.
It is found that time plays an important role in the cementation process because of the longer the time, the higher the copper recovery efficiency [16]. Over a period of 3 to 15 minutes, the copper recovery efficiency increased rapidly from 31.26 to 90.12%. However, the period from 15 to 25 minutes, the performance increase is not much. This is due to the amount of copper powder on the surface of the cast iron particles which interferes the cementation process. In addition, cast iron can be dissolved not only by cementation but also by iron corrosion in acidic solutions [14]. Therefore, the number of cast iron particles also needs to be adjusted to improve efficiency in this process.
4.Conclusions
The nix grain waste is treated and recycled by melting into cast iron in the electric arc furnace. Analytical results of the chemical composition of the cast iron and slag pattern showed that the quality of cast iron was satisfactory. The content of heavy metal elements in the slag is still very low, so it can be discharged into the environment. In addition, the cast iron pattern from nix grain waste can be applied in mechanics to manufacture a number of products such as metal fences or metal pads...The research results have great meaning in developing metallurgical technology and reducing environmental pollution. Especially, this study promotes research directions for treatment and recovery of wastes in the industries.
Acknowledgment: This study was supported by the Vietnam Academy of Science and Technology with the project: "Completing the recycling technology of nix grain waste or copper slag into granular cast iron as raw materials for the cementation process of copper powder in hydrometallurgical copper sulphate solution from ore or waste containing copper – Code: UDSXTN.02/21-22.
References:
- Qi.C, Weinell.E.C, Dam-Johansen.K, Wu.H: Journal of Environmental Management. 300 (2021) 113714. DOI: 10.1016/j.jenvman.2021.113714.
- Mitra.S, Chakraborty.J.A, Tareq.M.A, Emran.B.T, Nainu.F, Khusro.A, Idris.M.A, Khandaker.U.M, Osman.H, Alhumaydhi.A.F, Simal-Gandara.J: Journal of King Saud University - Science. 34 (2022) 101865. DOI: 10.1016/j.jksus.2022.101865.
- Sun.W, Wang.Q, Yue Zhou, Wu.J: Applied Energy. 268 (2020) 114946. DOI: 10.1016/j.apenergy.2020.114946.
- Costa.D.C, Lustig.S, D’Angelo.V.M, González.A.G: Journal of Environmental Chemical Engineering. 8 (2020) 103989. DOI: 10.1016/j.jece.2020.103989.
- D’Ippolito.A.S, Catherine Especel.C, Vivier.L., Epron.F, Pieck.L.C : Applied Catalysis A: General. 469 (2014), Pages 541-549. DOI: 10.1016/j.apcata.2013.06.009.
- Alipour.Z, Rezaei.M, Meshkani.F: Journal of Industrial and Engineering Chemistry. 20 (2014), Pages 2858-2863. DOI: 10.1016/j.jiec.2013.11.018.
- Mackenzie.D.J: Advances in Inorganic Chemistry and Radiochemistry. 4 (1962), Pages 293-318. DOI: 10.1016/S0065-2792(08)60270-8.
- Lin.K, Shen.Z, Liang.Q, Dai.Z, Xu.J, Guo.X, Liu.H: Fuel. 307, 1 January (2022) 121796. DOI: 10.1016/j.fuel.2021.121796.
- Choi.S.J, Park.J.T, Min.J.D, Sohn.L: Journal of Materials Research and Technology. 15 (2021), Pages 1382-1394. DOI: 10.1016/j.jmrt.2021.08.126.
- Jung.I, Lehmann.J, Jak.E. Treatise on Process Metallurgy. 2 (2014), Pages 675-798. DOI: 10.1016/B978-0-08-096984-8.00032-X.
- Masindi.V, Muedi.L.K, Environmental Contamination by Heavy Metals, Book Heavy Metals (2018).
- William.F.S, Hashemi.J, Foundations of Materials Science and Engineering (4th edition) (2006).
- DeGarmo.E.P, Black.J.T, Kohser.A.R, Materials and Processes in Manufacturing (9th edition) (2003).
- Singh.R, Agrahari. S, Yadav.D.S, Kumar.A: Materials Science and Engineering: A. 812 (2021) 141105. DOI: 10.1016/j.msea.2021.141105.
- Solfiti. E, Berto.F: Procedia Structural Integrity. 26 (2020), Pages 187-198. DOI: 10.1016/j.prostr.2020.06.022.
- Wu.L, Li. Y, Cao.H, Zheng.G: Journal of Hazardous Materials. 299 (2015), Pages 520-528. DOI: 10.1016/j.jhazmat.2015.07.053.