LIGHTWEIGHT STRUCTURAL CONCRETE WITH THE USE OF A DIATOMITE-BASED AGGREGATE
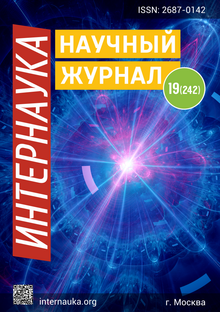
LIGHTWEIGHT STRUCTURAL CONCRETE WITH THE USE OF A DIATOMITE-BASED AGGREGATE
Aidana Berikbolova
Assistant, Master of Technical Sciences, Satbayev University,
Kazakhstan, Almaty
ABSTRACT
This article presents the results of research on the development of lightweight structural concrete with the use of aggregate based on diatomite from the Utesay deposit in the Aktobe region. A light aggregate is obtained by granulating a mixture of diatomite with burn-out additives and firing at 800 oC. The strength of the diatomite aggregate under compression in the cylinder is 8.2-11.8 MPa. The compositions of raw materials mixtures were calculated and samples were made-cubes of light structural concrete. The products were cured for 7 days under normal conditions in a bath with a water gate (20 + / -2 oC, humidity 95%). The compressive strength of the concrete samples was 12.74-12.77 MPa, the average density was in the range of 1740-1800 kg / m3, the thermal conductivity coefficient is 0.8-0.83 W / m3. The values of the properties of the obtained concrete samples meet the requirements of GOST 25820-2014 Light concrete. Technical conditions.
Keywords: diatomite, aggregate, light structural concrete, strength, bulk density.
One of the significant places, in reducing the mass of the structure, belongs to light concrete and their main component - porous aggregates. The problem of light filler remains very urgent for modern construction. Porous aggregates and light concretes based on them are destined to play a more significant role in the construction business of the future [1].
This article presents the results of research on the development of lightweight structural concrete compositions using a lightweight aggregate based on diatomite from the Utesayskoye deposit of the Aktobe region. Diatomites of the Utesayskoye deposit are light gray, porous, have the following chemical composition, wt.%: SiO2 65.88-83.65; Al2O3 8.36-14.00; Fe2O3 2.35-6.9; CaO 0.5-1.5; MgO 0.62-1.64; SO3 0.1-3.0; pp 4.59-12.1. Properties of diatomites: true density 2200 kg/m3; bulk density 400-600 kg /m3, porosity 72-82%, and organogenic impurities and moisture 11%. According to X–ray phase analysis, they contain β - quartz, kaolinite, montmorillonite and magnetite. The bulk of the diatomite is an amorphous substance and is not detected on the X-ray.
Earlier, I conducted research on the development of compositions of light aggregates using natural diatomite from the Utesayskoye deposit of the Aktobe region [2,3]. Table 1 shows the compositions and properties of light fillers based on diatomite obtained by firing at a temperature of 800 ° C for 1 hour.
Table 1.
Compositions and properties of diatomite-based light filler samples
№ |
Compositions of light filler |
Bulk density, kg/m3 |
Compression strength in the cylinder, MPa |
1 |
Diatomite – 100 % |
579 |
12,5 |
2 |
Diatomite – 95% Sawdust – 5% |
555 |
11,3 |
3 |
Diatomite – 90% Sawdust – 10% |
488,5 |
10,3 |
4 |
Diatomite – 85% Sawdust – 15% |
422 |
8,2 |
5 |
Diatomite – 97% Hard coal – 3% |
563 |
11,8 |
6 |
Diatomite – 95% Hard coal – 5% |
553 |
10,5 |
7 |
Diatomite – 93% Hard coal – 7% |
533 |
8,9 |
As can be seen from the data given in Table 1, a light filler made of diatomite without additives has high mechanical properties when compressed in a cylinder. In order to reduce the bulk density of the diatomite aggregate, sawdust and coal were added to the mass. The most effective burnout additive is sawdust, which, depending on the amount, reduces the density of the filler in comparison with the filler based on pure diatomite by 24-192 kg/m3. The addition of coal reduces the bulk density of the filler based on pure diatomite by 16-59 kg/m3. Burnout additives significantly reduce the strength of aggregates during compression in the cylinder, however, these indicators are quite high and meet the requirements of regulatory documents [4].
On diatomite aggregates obtained with burnout additives, the calculation of light concrete compositions was performed according to the method given in the literature [5]. Two compositions of light structural concrete were calculated. To calculate the composition of concrete, diatomite aggregates of compositions 3 and 6 were used (Table 1), which have the lowest values for bulk density.
Calculations have shown that the preparation of 1 m3 of light concrete requires:
1 composition – Portland cement 385 kg; filler (diatomite with sawdust) – 308.8 kg; quartz sand – 948.2 kg; water – 212 liters; calcium chloride – 11.6 kg;
2 composition – Portland cement 385 kg; filler (diatomite with coal) – 329.6 kg; quartz sand – 927.4 kg; water – 212 liters; calcium chloride – 11.6 kg.
Samples of light concrete were prepared based on the calculation of the composition per 1 m3 of concrete. Concrete samples were prepared in the form of cubes of standard sizes 10x10x10 cm, with a volume of 1000 cm3. To prepare the concrete mixture for such a volume, the raw materials components were recalculated.
After weighing, according to the calculation, the raw materials were mixed in dry form for 1.5-2 minutes, then water was added and mixed again until a homogeneous mixture was obtained. The resulting mixture was placed in pre-oiled metal molds and subjected to vibration on a laboratory vibrating table for 10-12 seconds. Concrete samples were kept in a metal mold for 10-12 hours, then released from the molds. Further hardening of the products was carried out at room temperature for 7 days in a bath with a water gate, then the average density and strength of concrete were determined.
Table 2.
Properties of light concrete samples with the use of aggregates based on diatomite
№ |
Name |
Average concrete density, kg/m3 |
Compressive strength, MPa, (after 7 days of hardening) |
Coefficient of thermal conductivity, λ, W/m0C |
1 |
Lightweight concrete with the use of a diatomite-based aggregate with sawdust |
1740 |
12,74 |
0,8 |
2 |
Lightweight concrete with the use of a diatomite-based aggregate with coal |
1800 |
12,77 |
0,83 |
Figure 1 shows photographs of concrete samples based on diatomite aggregates obtained by firing with additives of sawdust and coal.
|
|
a |
a/ |
|
|
b |
b/ |
Figure 1. Samples of light concrete obtained using diatomite-based aggregates with sawdust and coal after compression tests
а – a cube of concrete with a diatomite filler with the addition of coal, а/ – the structure of this concrete; b – a cube of concrete with diatomite filler with the addition of sawdust, b/ – the structure of this concrete.
As can be seen in the photos, in the structure of concrete samples, the aggregate is unevenly distributed in its volume, and not destroyed granules are also visible, which indicates their high strength. In our opinion, with a more homogeneous structure and 28-day hardening of concrete, its strength index would be much higher.
According to the data given in Table 1, the properties of concrete samples fully meet the requirements of the regulatory document [6], which states that structural concrete must meet the following basic requirements:
- grade for average density not higher than D 2000;
- compressive strength of at least 12.5 MPa.
At the same time, the compressive strength indicators of our structural concrete samples are given after 7 days of hardening. According to [7], the theoretical strength of concrete after 28 days of age is 1.5 times higher than the strength of concrete at 7 days of age or is 60% of 28 days of strength. In addition, according to this source, the strength of concrete exactly corresponds to the dynamics of changes in the Mantissa of decimal logarithms and is determined by the formula: n = 100 (lg (n) / lg (28)), where n is the day on which to determine the strength of concrete (at least 3 days).
In accordance with that formula , the strength of concrete at the age of 7 days can be recalculated by the 28 - day strength according to the formula:
Rc (28) = Rc (7) (lg 28/lg 7)
where: Rc (28) и Rc (7) – compressive strength of concrete at 28 and 7 days of age.
After recalculation of concrete strength from 7-day to 28-day, the following indicators were obtained:
- at a value 1.5 times higher, the 28-day strength was 19.11 MPa and 19.16 MPa, respectively;
- with a value 60% higher, the 28-day strength was 21.2 MPa and 21.3 MPa, respectively;
- when calculating the dynamics of the change in the Mantissa of decimal logarithms, the 28-day strength was 21.8 MPa and 21.9 MPa, respectively.
The calculated values of strength indicators obtained, according to three types of calculations, are close and correspond to the concrete grade M 200 and class B15.
The coefficient of thermal conductivity of the resulting concrete is almost similar to the coefficient of thermal conductivity of expanded clay concrete with a density of 1600-1800 kg/m3 [8].
Thus, with 28 daily hardening under normal conditions (20 + / -2 OC and 95% humidity), with the use of diatomite aggregate, it is possible to obtain lightweight structural concrete M 200, on the basis of which it is possible to produce enclosing reinforced concrete structures for the construction of industrial and civil buildings.
References:
- Makridin N.I., Maksimova I.N. Iskusstvennyye poristyye zapolniteli i legkiye betony. - Uchebnoye posobiye. - M .: Penza, PGUAS, 2013. - 324s.
- Zhuginisov M.T., Berikbolova A. Legkiy zapolnitel' na osnove diatomita // Materialy Mezhdunar. nauch.- prakt. konfer., posvyashchennoy 120-letiyu Akademika K.I. Satpayeva i 85-letiyu obrazovaniya KazNITU: Innovatsionnyye tekhnologii - klyuch k uspeshnomu resheniyu fundamental'nykh i prikladnykh zadach v rudnom i neftegazovom sektore ekonomiki RK. KazNITU. - 2019. S.889-893.
- Zhuginisov M.T., Berikbolova A. Energoeffektivnyy legkiy zapolnitel' na osnove diatomita. // III mezhdunarodnaya nauchno-prakticheskaya konferentsiya. Kachestvo. Tekhnologii. Innovatsii. Novosibirsk. - 2020. S.126-130.
- GOST 32496 -2013 «Zapolniteli poristyye dlya legkikh betonov. Tekhnicheskiye usloviya ».
- Skramtayev B.G., Burov V.D., Panfilova L.I., Shubenkin P.F. Primery i zadachi po stroitel'nym materialam. M .: Vysshaya shkola. - 1970. - 232 s.
- GOST 25820-2014 Betony legkiye. Tekhnicheskiye usloviya.
- Prochnost' betona v vozraste 7 sutok. Stroymaterialy. mstyle-fur.ru. sevparitet.ru/raznoe/prochnost-
- Koeffitsiyenty teploprovodnosti stroitel'nykh materialov.