CHEMISTRY EFFECT OF TEMPERATURE ON PHASE CHANGE, GRAIN SIZE AND SHRINKAGE OF 0.76(Bi0.5Na0.5)TiO3 – 0.24SrTiO3
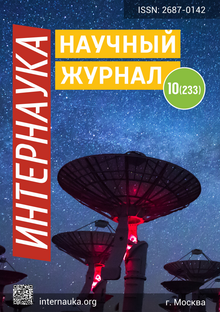
CHEMISTRY EFFECT OF TEMPERATURE ON PHASE CHANGE, GRAIN SIZE AND SHRINKAGE OF 0.76(Bi0.5Na0.5)TiO3 – 0.24SrTiO3
Nguyen Ba Phuong
M.S, Institute of Materials Science – Vietnam Academy of Science and Technology,
Vietnam, Hanoi
Nguyen Thi Hong Nhung
M.S, Sao Do University,
Vietnam, Haiduong
Mac Thi Nguyen
M.S, Sao Do University,
Vietnam, Haiduong
Nguyen Thi Lieu
M.S, Sao Do University,
Vietnam, Haiduong
Ngo Huu Manh
Ph.D, Sao Do University,
Vietnam, Haiduong
ABSTRACT
0.76(Bi0.5Na0.5)TiO3 – 0.24SrTiO3 was prepared by treating a common oxide mixture. SEM analysis method showed an increase in grain size with increasing temperature. With the calcination temperature of 550oC, 750oC, 850oC and 950oC, the grain sizes ranged from 200-250 nm, 1-1.5 µm, 2-2.5 µm and 3-4 µm respectively. The temperature dependence of the displacement shows an additional contribution from the structural transition (rhombohedra–tetragonal), which will have some relevance for the existence of morphological phase boundaries.
Keyword: Lead-free piezoelectric materials, phase change, grain size, shrinkage.
1. Introduction
Currently, the most commonly used piezoelectric materials are lead zirconate titanate (PZT)-based materials [1-3]. PZT is used due to the development of science and technology, so it causes the amount of lead oxide and lead zirconium titanate to leak into the environment more and more over the life of the material. This occurs during sintering when the excess lead oxide in the original oxide mixture is evaporated [4]. In addition, mechanical processing, recycling and wastewater also release lead into the environment.
The use, storage, recycling and handling the devices that contain lead- piezoelectric materials has become of great concern. Especially as they are now widely used in the medical and consumer products such as cars, audio equipment and medical equipment. Although PZT ceramic materials have outstanding advantages of excellent electrical properties and little dependence on temperature, the demand for lead-free piezoelectric materials is constantly increasing due to international environmental regulations which limit the use of lead-containing materials [5,6].
Barium titanate (BT), bismuth sodium titanate (BNT), piezoelectric ceramic (KxNa1-x)NbO3 (KNN) and K1/2Na1/2NbO3-LiTaO3 (KNN-LT) represent lead-free piezoelectric materials with structural perovskite architecture. Barium titanate is expected in this group of materials, but the low Curie temperature of BT(~ 135oC) and unstable phase transition, so limit the range of BT's use. Meanwhile, bismuth-based lead-free piezoelectric materials, specifically bismuth sodium titanate (BNT) system, have received much attention and have been extensively studied for many years due to its excellent electrical properties. BNT has a rhombic symmetry at room temperature [7], a relatively s strong ferroelectricity of 38 µC/cm2, a high Curie temperature of 320°C [8.9], and a coercive field of 73kV/cm at room temperature [9, 10]. Along with that, the solid solution of this system with ZrTiO3 that have the good electromechanical properties is expected to replace the lead-containing piezoelectric material PZT.
2. Experimental procedure
2.1. Equipment
Figure 1. Vacuum drying cabinet
Figure 2. Furnace
Figure 3. Hydraulic press
2.2. Experiment
Lead - free piezoelectric ceramic sample 0.76(Bi0.5Na0.5)TiO3 – 0.24SrTiO3 was prepared by means of a conventional solid – state reaction method. The component oxide and carbonate powders, Bi2O3 (99.9%), TiO2 (99.5%), Na2CO3 (99.8%) and SrCO3 (99.0%), were used as raw materials (High Purity Chemicals, Japan).
The raw materials were mixed in stoichiometric proportions by means of conventional ball – milling in ethanol using zirconia balls, then dried and calcined at 550°C, 750°C, 850°C and 950°C respectively for 2h to monitor phase change. The resultant powders were mixed with polyvinyl alcohol (PVA) binder and then pressed into 12 mm diameter green stem discs under 100 MPa axial pressure. Finally, it was sintered at 1050-1200°C for 4h. The density of the sintered samples was determined by the Archimedes method. The samples were polished were imaged via field – emission scanning electron microscopy and crystal structures were characterized by means of X – ray diffractometry (XRD - Institute of Materials Science).
3. Results and discussion
3.1. Effect of calcination temperature on phase composition
Figure 4 presents XRD patterns of 0.76(Bi0.5Na0.5)TiO3 – 0.24SrTiO3 ceramics. The analysis results showed that the pattern was unsatisfactory due to the lack of homogeneous phase formation and the appearance of undesirable phase components such as (Bi0.5TiO2, SrCO3, Bi0. 5Na0.5TiO3) at 550oC.
At the calcination temperature of 750oC, the X-ray diffraction pattern shows that the diffraction peaks of BNT-ST is multiphase and has not yet formed a homogeneous phase. However, we see that the desired phase has appeared interspersed with other phases.
At the calcination temperature of 850oC and 950oC, all the peaks in the X-ray diffraction pattern belong to the phase Bi0.5Na0.5Sr(TiO3)2.
Figure 4. X-ray diffraction pattern of 0.76BNT-0.24ST at 550oC; 750oC; 850oC and 950oC
3.2. Effect of temperature on grain size
|
|
(a) |
(b) |
|
|
(c) |
(d) |
Figure 5. SEM image of BNT-ST patterns at the calcination temperature
(a) - 550oC, (b) -. 750oC, (c) - 850oC, (d) - 950oC
Surface images of polished and thermally etched 0.76(Bi0.5Na0.5)TiO3 – 0.24SrTiO3 ceramics are displayed in Fig.5. From the SEM images, it can be seen that the synthesized patterns with relatively uniform particles. At the calcination temperature of 550oC, 750oC, 850oC and 950oC, the particle sizes fluctuate in the range of 200-250 nm, 1-1.5 µm, respectively. 2-2.5 µm and 3-4 µm. The reason is that the higher the calcination temperature, the faster the nucleation and growth rates increase, but the faster the growth rate increases, leading to larger seeds. In addition, the heat retention time (4 hours) is also the reason for the increased grain size
3.3. Effect of temperature on the shrinkage
During sintering, the 0.76BNT-0.24ST ceramic pattern will expand and its shrinkage will increase. On the other hand, when the temperature is increased, it will affect the ability to fill the holes, gradually increasing the density and reducing the shrinkage rate.
Figure 6. Effect of temperature on the shrinkage of BNT-ST patterns after sintering
When increasing the sintering temperature from 1050 - 1200oC, the shrinkage of the patterns increased from 13.02 to 14.53%. However, the optimal shrinkage for piezoelectric materials is from 14-16% because they will achieve the high density as well as the best electrical properties with this shrinkage. From the above results, it can be seen that, when sintering from 1150-1200oC, the BNT-ST sample achieves the desired target shrinkage of 14-16%.
4. Conclusions
0.76(Bi0.5Na0.5)TiO3 – 0.24SrTiO3 was prepared by means of a conventional solid – state reaction method. The material ceramic shows a single perovskite phase with a cubic structure. The average grain sizes increased with increasing temperature. This material ceramic have the competitive advantage of larger strain under lower operating field compared with other BNT – based lead – free piezoelectric ceramics. Therefore, we regard the ceramic as a promising candidate for for many practical applications.
References:
- X. Chao, Z. Yang, L. Xiong, Z. Li, Effect of addition of Ba(W0.5Cu0.5)O3 in Pb(Mg1/3Nb2/3)O3–Pb(Zn1/3Nb2/3)O3–Pb(Zr0.52Ti0.48)O3 ceramics on the sinteringtemper - rature, electrical properties and phase transition, Journal of Alloys and Compounds, 509 (2011) 512-517.
- G.H. Haertling, Ferroelectric Ceramics: History and Technology, The journal of the American ceramic, 82 (1999) 797-818.
- D.-Q. Zhang, D.-W. Wang, H.-B. Zhu, X.-Y. Yang, R. Lu, B. Wen, W.-Q. Cao, J.Yuan, M.-S. Cao, Synthesis and characterization of single-crystalline (K,Na)NbO3 nanorods, Ceramics International, 39 (2013) 5931-5935.
- C. Jiang, K. Zhou, X. Zhou, Z. Li, D. Zhang, Synthesis and characterization of Na0.5Bi0.5TiO3 platelets with preferred orientation using Aurivillius precursors, Ceramics International, 41 (2015) 6858-6862.
- J. Rödel, W. Jo , K.T.P . Seifert, E.M. Anton, T. Granzow, D. Damjanovic, Perspective on the development of lead‐free piezoceramics, J. Am. Ceram Soc. 92(2009) 1153–1177.
- M.F. Chris, E.B. John, J.B. Keith, Poling effect on d33 in textured Bi0.5Na0.5TiO3-based materials, Scripta. Materialia 68 (2013) 443–446
- G.A. Smolenskii, I.E. Chupis, Ferroelectromagnets, Soviet Physics Uspekhi, 25 (1989) 475-490.
- Y.-D.Hou, L.Hou, T.-T. Zhang, M.-K. Zhu, H. Wang, H. Yan, (Na0.8K0.2)0.5Bi0.5 -TiO3 Nanowires: Low-Temperature Sol-Gel-Hydrothermal Synthesis and Densifica -tion, Journal of the American Ceramic Society, 90 (2007) 1738-1743.
- T. Takenaka, K. Sakata, Dielectric, piezoelectric and pyroelectric properties of (BiNa)1/2TiO3-based ceramics, Ferroelectrics, 95 (1989) 153-156.
- I.P. Pronin, P.P. Syrnikov, V.A.Isupov, V.M. Egorov, N.V. Zaitseva, Peculiarities of phase transitions in sodium-bismuth titanate, Ferroelectrics, 25 (1980) 39.