METROLOGICAL ANALYSIS OF OPTICAL METHODS FOR MEASURING RAILWAY TRACK GEOMETRY PARAMETERS
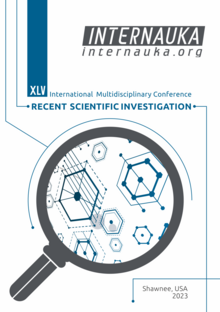
METROLOGICAL ANALYSIS OF OPTICAL METHODS FOR MEASURING RAILWAY TRACK GEOMETRY PARAMETERS
Dmitriy Roshchin
Candidate of science, senior Researcher, Research and Testing Center of Railway Troops,
Russia, Moscow
The existing methods of measuring the geometric parameters of the railway track and the technical means for their implementation are based on various physical principles and technical solutions. According to the principle of interaction with the rail gauge, all existing measurement methods are divided into two categories: contact, implying a mechanical connection of the measuring instrument with the rail, and non-contact, not having a mechanical connection with it [1]. Contact methods are quite simple to implement. They have become widespread due to the low cost and acceptable accuracy of contact measuring instruments. The main disadvantages, from the point of view of reliability, include the susceptibility of contact measuring instruments, as well as the communication lines connecting them to harmful mechanical and thermal influences, which leads to frequent and expensive failures and failures in control systems where they are used [2]. The presence of communication lines may interfere with rotating or moving components of the undercarriage of the track measuring control system. Limitations on the use of contact measuring instruments arise due to the inability to carry out measurements remotely, the complexity of transmitting measuring information to a device for processing it, as well as the complexity of automating the measuring procedure. These problems can be eliminated using non-contact measurement methods.
There are many situations in which it is necessary to measure the parameters of a railway track without having physical contact with it, or when such contact is simply impossible. For example, when assessing the condition of a damaged section of railway, in areas of occurrence of natural disasters or man-made accidents. Thus, for cases in which contact with a rail track is impossible or unacceptable, it becomes necessary to use non-contact methods, which, in turn, does not exclude their applicability along with contact measurement methods. The general advantage of contactless methods is the absence of mechanical impact on the track and negligible inertia, which avoids the main disadvantages inherent in contact methods. It becomes possible to obtain the necessary information at long distances, in any operating modes, in conditions of low and high temperatures or pressures, as well as in conditions of radiation or chemical contamination, etc. Non-contact methods exclude wear and breakage of mechanical elements of the measuring instrument at the points of contact with the track gauge, which increases the reliability of their application and measurement accuracy [3].
The choice of the measuring instrument largely determines the choice of the measurement method that is most suitable for it. The principle of operation of contactless methods is based on the sounding of the rail track by sound or electromagnetic waves [4-6]. There are the following non-contact measurement methods: optical based on physical phenomena (photometry, diffraction, interference, projection), holographic, laser, acoustic, magnetic and radio waves.
To measure the geometric parameters of the track gauge, optoelectronic meters are produced, the principle of operation of which is based on various methods: shadow projection, scanning, triangulation, television, interference, diffraction, correlation, structural illumination. Optical methods have become widespread. The most common are triangulation systems [7], which serve to determine the distance to the surfaces scattering light. The triangulation method is based on the property of the laser beam to propagate over long distances with virtually no scattering. The principle of operation of such a measuring system is that the laser illuminates a point, and the detecting device registers the light reflected from this point.
Figure 1. Principle of operation of the triangulation laser sensor:
1 – rail surface, 2 – laser emitter, 3 – photodetector, b – base distance
This method is characterized by high speed and accuracy of measurements. Typical accuracy values of such measuring equipment are on the order of tenths of a percent of the measured distance. The method has limitations on the measurement range and can be used as long as the light energy of the reflected scattered radiation incident on the photodetector matrix exceeds the value of its noise level.
Shadow projection and scanning methods are also used to determine the geometric dimensions of the rail track [8]. Figure 2 shows a diagram of the shadow projection system [9]. The meter includes optical and electronic units: a light source and a collimating lens O1, a photodetector module consisting of an O2 lens and a lens aperture А, as well as a photodetector matrix (PM).
Figure 2. Diagram of the shadow projection system of the rail
The sources of errors of the shadow projection method [10] are: aberrations of the optical system, focusing accuracy, the method of rail illumination (reflected or transmitted light, the degree of coherence of the light beam), reflecting properties of the rail surface (reflection and transmission coefficients, contrast, phase shift), the size and relative location of rail filaments and optical elements [11]. The use of shadow projection schemes with a parallel illuminating beam and a specialized telecentric lens makes it possible to increase the accuracy of determining the geometric parameters of the rail track. An important advantage of such systems is low sensitivity to vibrations, as well as low requirements for sensor positioning accuracy. Among the many known optical measurement methods, pulse and phase methods are the best mastered. The very short duration of pulses emitted by many types of lasers, in particular solid-state lasers, in the resonator Q-factor modulation mode and especially in the mode synchronization mode, combined with the high energy of such pulses, opened the way to the creation of a pulsed laser measurement method, which has now become very widespread.
The error in the time fixation of radiation pulses is mainly related to the reception of the reflected laser pulse. The signal power can vary by several orders of magnitude depending on the distance of the rail track and its reflection coefficient, the state of the radiation propagation medium layer. In addition, noise and interference from the receiving channel and the radiation propagation channel are superimposed on the signal. All this leads to strong distortions in the shape of the received signal and the occurrence of an error in fixing the moment of arrival of the pulse by the threshold device.
The estimation of the spatial range measurement zone can be carried out using the location equation:
,
where: РRC – received light power,
РTR, θTR – the power and divergence of the transmitted light,
Sref, Rref – the area and reflection coefficient of the surface of the rails,
θref – divergence of reflected light,
SRC – the area of the receiving aperture of the rangefinder,
τTR, τRC, τatm – transmittance of the transmitter, receiver and atmosphere.
The dependence of the range D depends more on the divergence of the light of the transmitter than on its power. At the same time, there is a significant functional limitation of the parameter θper, due to the error of the guidance system used: an excessive decrease in the divergence value can cause a miss. The latter circumstance is especially important for measuring the range of a rail track when the rangefinder is placed on a vehicle [12].
The phase method of measuring the propagation time of modulated laser radiation is characterized by a small measurement error. The pulse-phase method of distance measurement largely combines the advantages of phase methods in terms of measurement accuracy and pulse methods in terms of range [13]. At the same time, a sequence of radiation pulses is used as the probing signal of the light meter, and the time of passage of the distance to the rail track by the optical signal is measured by the phase method.
A significant disadvantage of optical methods is the high requirements imposed on the quality of the rail surface and measurement conditions [14]. When measuring the distance to scattering surfaces by the triangulation method, the angle of incidence of the laser beam does not significantly affect the result [15, 16]. In the case of determining the distance to the mirror surfaces of the rail, the influence of this angle becomes significant. At the same time, the limit of the measured distances increases significantly. However, a rather laborious angular calibration of the triangulation system is required to stabilize the non-zero angle of incidence of the laser beam [17]. Common disadvantages of optical measurement methods are: complexity, bulkiness and high cost of equipment; high energy consumption; high requirements for the quality of the rail surface and for the conditions of measurement (humidity, dustiness, etc.) [3]. In addition, laser radiation requires additional precautions and protection [18].
References:
- Rudenko D.F., Volkovets A.I., Gusinski A.V., Kostrikin A.M., Herasimionak A.O., Dzisiak A.B. The microwave vibration meter // 15th International Crimean Conference Microwave & Telecommunication Technology, Sevastopol, Ukraine. 2005, P. 829-830. Vol. 2. doi:10.1109/CRMICO.2005.1565159.
- Volkov YU.V. Datchiki dlya izmerenij pri proizvodstve elektricheskoj i teplovoj energii: uchebnoe posobie. – SPb.: VSHTE SPbGUPTD, 2019. 89 p.
- Volkovec A.I., Rudenko D.F., Gusinskij A.V., Kostrikin A.M. Radiovolnovyj beskontaktnyj metod izmereniya parametrov dvizheniya i vibracii // DOKLADY BGUIR. 2007. Vol. 20. No. 4. P. 58-64.
- Viktorov V.A., Lunkin B.V., Sovlukov A.S. Radiovolnovye izmereniya parametrov tekhnologicheskih processov. – Moscow: Energoatomizdat, 1989. – 208 p.
- Vahitov SH.YA., Kovatgin YU.A., Fadeev A.A., SHCHev'ev YU.P. Akustika. – Moscow: Goryachaya liniya – Telekom, 2009. – 660 p.
- Ivanov N.I. Inzhenernaya akustika. Teoriya i praktika bor'by s shumom. – Moscow: Logos, 2008. – 424 p.
- Liebe C.C., Coste K. Distance measurement utilizing image-based triangulation // IEEE Sensors Journ. 2013. Vol. 13. No. 1. P. 234-244. doi:10.1109/JSEN.2012.2212428.
- Demkin V.I., Litmanovich A.M. Optiko-elektronnaya izmeritel'naya sistema dlya opredeleniya prostranstvennogo polozheniya ob"ekta na osnove metoda tenevoj lokacii // Izvestiya vuzov. ELEKTRONIKA. 2011. Vol. 89. No. 3. P. 69–74.
- Lemeshko YU.A., CHuguj YU.V. Difrakcionnyj metod izmereniya diametrov krugovyh otrazhayushchih cilindrov // Avtometriya. 2005. Vol. 41. No. 6. P.3-12.
- Rozhdestvenskij D.S. Kogerentnost' luchej pri obrazovanii izobrazheniya v mikroskope \\ ZHurnal eksperimental'noj i teoreticheskoj fiziki. 1940. Vol. 10, No. 3, P. 305-330.
- Bystrov YU.A., Kolgin E.A., Kotlecov B.N. Tekhnologicheskij kontrol' razmerov v mikroelektronnom proizvodstve. – Moscow: Radio i svyaz', 1988. 162-166 pp.
- Stavrov A.A., Pozdnyakov M.G. Impul'snye lazernye dal'nomery dlya optiko-lokacionnyh sistem \\ Doklady BGUIR. 2003. Vol. 1. No. 2. P. 59-65.
- Mogil'nickij, B. S. Lazernye tekhnologii dlya precizionnyh izmerenij bol'shih dlin / B.S. Mogil'nickij // Kompetentnost'. 2020. No. 2. P. 49-53.
- Zak E. Kogerentnye svetovye metody izmereniya parametrov mekhanicheskih kolebanij // Zarubezhnaya radioelektronika. 1975. No. 12. P. 70-76.
- Mordasov M.M., Savenkov A.P., Safonova M.E., Sychev V. A. Beskontaktnoe triangulyacionnoe izmerenie rasstoyaniya do zerkal'nyh poverhnostej // Avtometriya. 2018. Vol. 54. No. 1. P. 80-88. doi:10.15372/AUT20180111.
- Mihlyaev S.V. Analiz opticheskih triangulyacionnyh sistem izmereniya profilya zerkal'noj poverhnosti // Avtometriya. 2005. Vol. 41. No. 4. P.78-91.
- Borisov V.N., Kirikov A.V., SHCHerbakov V.A. Patent № 2541704 C2 Rossijskaya Federaciya, MPK G01B 11/02. Sposob kalibrovki i nastrojki sistemy lazernyh datchikov i ustrojstvo dlya ego osushchestvleniya nablyudeniya.
- Rahmanov B.N., Kibovskij V.T. Lazer. Vse zhe kakogo on klassa opasnosti? // Fotonika. 2015. Vol. 53, No. 5. P. 42–49.