THE EFFECT OF PARTICLE SIZE AND MORPHOLOGY ON THE SINTER ABILITY OF Fe-Cu-Sn-Ni COMPOSITES MADE BY POWDER METALURGY
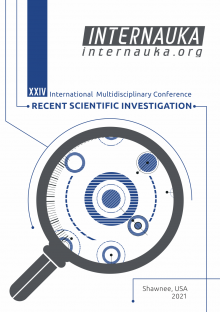
THE EFFECT OF PARTICLE SIZE AND MORPHOLOGY ON THE SINTER ABILITY OF Fe-Cu-Sn-Ni COMPOSITES MADE BY POWDER METALURGY
Nikoloz Loladze
PhD, Professor, Georgian Technical University,
Georgia, Tbilisi
Medea Tserodze
PhD, Associate Professor, Georgian Technical University,
Georgia, Tbilisi
Zurab Avalishvili
PhD, Assistant Professor, Georgian Technical University,
Georgia, Tbilisi
Iura Dzidzishvili
Master, Georgian Technical University,
Georgia, Tbilisi
Keywords: Powder metallurgy, particle size, morphology, sinter ability.
Background
The need for composite materials has become a necessity for modern technology, due to the improved physical and mechanical properties. Metal matrix composites (MMC) have been developed in recent years, among them are diamond composites, that have very wide applications in the various fields. Nowadays, most of MMC are produced by the traditional rout of hot pressing or conventional sintering.
Depending on the application field, the metal matrix must have a certain set of physical, physicochemical and physic mechanical characteristics. The acquiring certain properties by the metal composition, largely depends on the technical process of its formation. Therefore, the work, that are directed to further improving the technology of materials are actual.
Sintering appears to be one of the main technological operations of powder metallurgy. In this operation, complex physical and physicochemical processes take place, including diffusion, which can be considered as fundamental part in the formation of the structure and operational properties of a powder product, especially when using multicomponent materials.
Results show that the size and shape of particles has significant influence on the sintering process. Samples prepared from spongy powder had much greater shrinkage than the ones from produced from spherical powder [1]. In general, sinter ability of powder compacts is determined by several factors, namely mean particle size, size distribution, and shape of particles as well as sintering conditions (P-T-τ). Furthermore, the particle size and morphology influences the sintering process itself in addition to properties of readymade parts [2,3].
Considering the mean particle size, particles with smaller mean size sinter quickly as compared to the relatively coarser particles. The better sintering characteristics of the relatively smaller particles can be attached to the larger specific surface area of the smaller particles, which leads to increased surface energy and favors subsequent sintering.
Powder materials used in various branches of technology are in most cases multi-component systems. The formation of an alloy of the required phase composition, mainly, occurs directly during sintering. The main distinguishing feature of such materials is the presence of inequality in the concentration of components in various volumes of the original powder body (chemical composition gradient).
The sintering process of dissimilar particles appears to be more complicated; simultaneously with self-diffusion, heterodiffusion must occur, which provides concentration equalization.
It’s known that the technological factors influencing sintering process include the properties of the initial powders, the pressure and temperature of formation, the duration and atmosphere of sintering. Activated sintering is the process of sintering powders under the influence of chemical and physical factors causing the intensification of sintering. Physical methods of activated sintering are associated, first of all, with an increase in the dispersion of the powder and the defectiveness of the crystal lattice of the substance of its particles. Intensive grinding of particles increases their total surface, increasing the reserve of excess energy of the powder and increasing the thickness of the "damaged layer". This, in return, contributes to the activity of such mass transfer mechanism as "surface diffusion".
It’s known that any type of grinding is mechanical activation, the energy reserve of the ground substance increases under the action of external forces. In modern production, for the implementation of these operations, various types of mills are most often used. Grinding conditions have a significant effect on particle size, morphology and defectiveness.
In the process of powder dispersing, not only the particles grinding and an increase in their specific surface occurs, but also the formation of defects in the crystal structure, which affect the rate of diffusion processes. In accordance with the vacancy theory of diffusion [4], the diffusion coefficient is proportional to the vacancy concentration:
D = ξ* D’;
where ξ*- the vacancy concentration:
The main purpose of this work is to investigate the influence or to establish the effect of shape and dispersion in particle size distribution on sinter ability of four component compositions.
Experiments were carried out to establish the role of initial powder dispersion and particles morphology on the kinetics of the sintering process. For this purpose, Fe-Cu-Sn-Ni (47%-32%-8%-13%) was used. It should be mentioned, that system close to Fe-Cu-Sn-Ni composition by the consistency (51%-32%-8%-9%) is well-known and reviewed in the scientific literature [5,6].
Methods
Powders of iron “PJ1 М2”, copper “МPS-1” (Cu - 99.5%), nickel “PNE-1”, tin “PО -1” (metalls powders grade in Russian), were used as starting materials for the manufacture of metal compositions for sintering. Content of impurities in metal powders and ingots are no more than 0.5% mass. Iron powder with an initial grain size of 200/100 µm. was subjected to mechanical treatment in a stainless steel ball mill using alloy steel grinding balls 12 mm in diameter. The weight ratio of balls to powder was 10:1.
After ball milling the powder were tested for particle size and shape. Subsequently, particle size was measured using Laser Diffraction Particle Size Analyzer (Malvern Panalytical Mastersizer 2000, Japan). The microstructure and morphology of the powder were observed by scanning electron microscopy (SEM microscope TM3030Plus, Hitachi).
Mixtures of metal powders were mixing during 30min. in industrial mixer. The sintering process was performed in cylindrical molds by hot pressing. The developed sample (sinters) was about 15mm in diameter and 9mm in height. Graphite CPV 14814000 was used as hot pressing molds material. The process was conducted in conditions of pressure - 40 MPa, holding time at the sintering temperature - 2 min and temperature - 780 - 8000C.
Density calculation of sintered composites were performed by formula:
Y = m1 · ywater / m1 – m2
where m1 is the mass of the sample in air, g; m2 is the mass of the sample in water, g; y is the density of water at the measurement temperature, g/cm3. The mass was measured with an accuracy of 10-4g.
Also, the hardness of sintered samples was characterized by the Rockwell B scale.
Result and Conclusions
For revealing the difference and to establish the role of the initial powder dispersion and morphology under hot sintering conditions special experiment were carried out. For this purpose, Fe –Cu – Sn – Ni (47% – 32% – 8% – 13%) system was used. In this case, the dispersion and morphology of the main component, Fe, were changed. The 200/125 and -63 µm fractions of the original iron powder (Water atomized) was used, as well as activated by ball milling for 40 -80 h. the initial powder of grain size 200/100 µm.
Powder characteristics: size distribution, mean particle size, specific surface area and morphology structure, as well as, density value and hardness of sintered samples are presented in tables 1 and 2.
Table 1.
Milling time and physical characteristics of iron powder
## |
Initial size, μm |
Milling time, h |
Average mass diameter, D |
Min. and max. mass diameters, μm |
Specific surface area, m2/gr |
||
1 |
200/100 |
0 |
116 |
70 - 190 |
0.055 |
||
2 |
-63 |
0 |
43 |
20 – 82 |
0.287 |
||
3 |
200/100 |
30 |
117 |
16 - 157 |
0.073 |
||
4 |
200/100 |
40 |
58,4 |
13 - 116 |
0.292 |
||
5 |
200/100 |
60 |
44 |
11 - 87 |
0.309 |
||
6 |
200/100 |
80 |
30.4 |
6.9 - 75 |
0.421 |
Picture 1. Millng time 0 h. 200/100 Picture 2. Millng time 0 h. -63
Picture 3. Millng time 30 h Picture 4. Millng time 40 h.
Picture 5. Millng time 60 h Picture 6. Millng time 80 h.
In Table 1 are presented the experimental results on the change in the physical properties of the experimental iron powder of the initial grain size 200/100 after the process of techno activation - grinding in a ball mill (ball milling) at a duration of 0, 30, 40, 60 and 80 h. It was found that as the grinding time increases, the shape of the initial particles of iron powder changes and from spheroidal (Table 1, sample 1,2) becomes more and more flat and flaky. The study showed, that during milling particles are repeatedly flattened, work-hardened and fractured, and sometimes welded together. After 40 hours and especially 80 hours of milling they show flaky shape (Table 1, sample 4,6).
Table 2.
Physical properties of Fe powders, sinters densities and hardness numbers
## |
Size, μm Milling time, h |
Specific surface area, S,m2/g |
Density ρ, g/sm3 |
HRB |
Size distribution |
1 |
200/100 |
0.0553 |
8.33 |
84-89 |
|
2 |
-63 |
0.287 |
8.00 |
93 |
|
3 |
40 hour |
0.292 |
8.22 |
93 |
|
4 |
80 hour |
0.457 |
8.23 |
103 |
|
Table 2 shows data for the Fe-Cu-Sn-Ni system when the initial charge is a mixture of individual powders of iron, copper, nickel and tin. Iron was used in one case in its original state i.e. water atomization without mechanical activation of various fractions (200/100 and -63 μm), accordingly, the shape of the particles is spheroidal (Table 1, samples 1,2). In another case, the powder was mechanically activated (Table 1, sample 4,6).
In both cases, the granularity of the rest of the powders (Cu, Sn, Ni) used in the sintering process had the same granularity of -50 µm. The samples 1,2 in table 2 presents the data of sinters using iron powder with a grain size of 200/100 and -63 microns, that did not undergo mechanical activation. Despite the Specimens sintered in the presence of coarse iron powder with a minimum specific surface area (0.0553 m2 /g), have high density values ρ = 8.33 g /cm3, they are characterized by a minimum hardness and a significant spread in the value, which shows a highly inhomogeneous distribution of structure and phase. The use of more dispersed iron powder of -63 μm, with the less average mass diameter and an increased specific surface at the same time the increased hardness of the sinters was observed, while the value of the density of the sinters is still minimal. This is most likely because of increased porosity due to a significant decrease in the size of the spheroidal particles. This contributes to a sharp increase in the number of small pores due to the geometric factor of the particle. After the activation of iron powder, the particles (samples 4 and 6 of Table 1) take the form of well-known morphology [7]. With an increase in the activation time, the value of the specific surface of the powder increases, the average mass diameter decreases, a high density value is observed, and the hardness and homogeneity of the sintered samples increase significantly (table 2, samples 3,4). The data obtained are in good agreement with the general laws of the theory of powder metallurgy - the higher the dispersion of the initial powders, the higher the sinterability of the composition.
In addition to the abovementioned reasons - increasing the specific surface of the powder and decreasing the average mass diameter – in our opinion one of the main factors for improving the sinterability of mechanically activated powder is its acquired morphology (shape) of particles.
It’s well known [8] that the nature of the packing of powder particles is its important characteristic, since it largely determines the filling of the molds and thereby shrinkage during sintering. So, for uniform sized spherical particles filling density of volume varies from 0.6 to 0.64. This corresponds to a coordination number of 6 - 7 (the number of contacts of particles with neighbors). For irregular shaped particles, the relative packing density is about 0.3 and even lower for very fine powders of irregular shape. With such a relative density, the coordination number is within the range of 2 - 4. The more developed surface of the powder is and more deviated from the regular shape - the lower is the packing density. The packing density increases as the particle surface smoothens and approaches the rounded equilibrium shape. It should be noted, that those particles, which slightly differ in shape from a sphere, can have maximum packing density. So, the cubes in a certain order can be packed with a density of 100%. It can be assumed that the flattened, flake-like shape of the powders, which are obtained after mechanical activation of the spheroidal iron powder, will exceed the spheroidal ones in terms of packing density, i.e. packing density for the initial stages of the sintering process ≥0.64. An increased packing density and, accordingly, an increase in the contact surfaces, in addition to other factors (for example, the defectiveness of the surface layer of particles) will improve the parameters of the sintering process. This phenomenon has been observed in presented research results.
The work has been carried out under the grant of Shota Rustaveli National Science Foundation of Georgia (Contract AR - 18 -1911).
References:
- Sanches F., Bolarin A. M., Molera P., Mendoza J. E. and Ocampo M. Relationship between Particle size and Manufacturing Processing and Sintered Characteristics of Iron Powders, Revista Latinoamerica de Metalurgia y Materiales, Vol. 23 #1, p.35-40.
- Poquillon D., Lemaitre J. et al. Cold Compaction of Iron powders-relations between powder morphology and mechanical properties. Part II; Bending Test: results and analysis. Powder Technology, 126 (2002), pp. 75-84.
- Mehdi Rahimian, Naser Ehsani, Nader Parvin, Hamid reza Baharvandi. The effect of particle size, sintering temperature and sintering time on the properties of Al-Al203 composites, made by powder metallurgy, Journal of Materials Processing Technology,. Journal of Materials Processing Technology, 2009, p.1-14.
- Sheleg V.K., Kovchur A.S., Moskalets R.A. Theoretical analysis of diffusion during sintering powder materials. J.”Chemical Technology and Ecology”, #29, 2015, p.114-120. (in Russian).
- Mechnik V.A. Production of Diamond – (Fe-Cu-Ni-Sn) composites with high wear resistance. J. Powder Metallurgy and Metal Ceramics. 2014, 52, 9, p.577-587.
- Zaitsev A. A., Sidorenko D. A., Levashov E. A., Kurbatkina V. V., Rupasov S. I., Andreyev V. A. and Sevast’yanov P. V. Development and application of dispersion–hardened binder based on Cu–Ni–Fe–Sn alloy for cutting tools from superhard materials. J. Superhard Materials. 2012, 2, p75-88. (in Russian).
- Konstanty J., Romunski A. New Nanocrystalline Matrix Materials for Sintered Diamond Tools. J. Materials Science and Applications. 2012, 3, p.779-783.
- Girshov V.L., Kotov S.A., Tsemenko V.N. Modern Technology in Powder Metallurgy. “Politechnikal University” Sank-Petersburg, 2010, 384p. (in Russian).