ЭКОЛОГИЧЕСКИЕ ВОПРОСЫ КОМПЛЕКСНОЙ ПЕРЕРАБОТКИ ЗОЛЫ
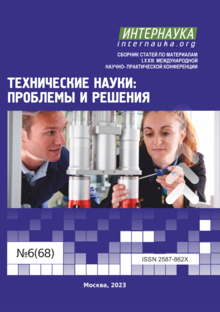
ЭКОЛОГИЧЕСКИЕ ВОПРОСЫ КОМПЛЕКСНОЙ ПЕРЕРАБОТКИ ЗОЛЫ
Жолдасбай Ержан
д-р PhD, ведущий научный сотрудник, Satbayev University,
Казахстан, г. Алматы
Аргын Айдар
д-р PhD, старший научный сотрудник, Satbayev University,
Казахстан, г. Алматы
Досмухамедов Нурлан
канд. техн. наук, проф., Satbayev University,
Казахстан, г. Алматы
АННОТАЦИЯ
Угольные электростанции ежегодно производят большие объемы золы. 50% летучей золы, произведенной в США, утилизируются в различных областях хозяйства. Зола содержит опасные микроэлементы (As, B, Cr, Mo, Ni, Se, Sr и V), которые оказывают негативное влияние на окружающую среду из-за потенциального выщелачивания кислотными дождями и грунтовыми водами.
Существующие методы переработки золы позволяют извлекать незначительные количества ценных компонентов. В то же время по вещественному составу золу можно рассматривать как самостоятельное комплексное сырье для извлечения целого спектра ценных металлов. Зола выгодно отличается от обычных месторождений полезных ископаемых, находится на поверхности и не требует больших затрат на добычу.
В работе разработана технология по переработке золы с извлечением ценных металлов в товарные продукты. Установлены оптимальные технологические параметры технологии. Показано возможность комплексной переработки золы с получением товарных продуктов.
Ключевые слова: уголь, зола, переработка, технология, алюминий, металлы примеси, экология.
Введение
Угольные электростанции ежегодно производят большие объемы золы. 50% летучей золы, произведенной в США, утилизируются в различных областях хозяйства. Большая часть золы расположена на полигонах и зольных лагунах. Зола содержит опасные микроэлементы (As, B, Cr, Mo, Ni, Se, Sr и V), которые оказывают негативное влияние на окружающую среду из-за потенциального выщелачивания кислотными дождями и грунтовыми водами. Зола –крупнейший вид отхода. Ежегодно в США производится более 100 миллионов тонн. Объемы ежегодного выхода золы в разрезе развитых стран в млн. т: Индия – 112, Китай – 100, Германия – 40 и Великобритания – 15 [1, 2, 3].
В Российской Федерации действует более 170 тепловых электростанций (ТЭЦ) на угольном топливе, в которых сжигается ежегодно 650 млн. т угля с образованием 300 млн. т золы. Под хранение золошлаковых отходов в России отчуждено более 20 тыс. км2 земельных участков, на которых находится 1,3–1,5 млрд. т золы [4].
Существующие методы переработки золы [1-6] позволяют извлекать незначительные количества ценных компонентов. В то же время по вещественному составу золу можно рассматривать как самостоятельное комплексное сырье для извлечения целого спектра ценных металлов. Зола выгодно отличается от обычных месторождений полезных ископаемых, находится на поверхности и не требует больших затрат на добычу. Накопленные объемы золы очень значительны, и с каждым годом продолжают расти в геометрической прогрессии.
Химический состав золы зависит от типа сжигаемого угля и может варьировать в широких пределах по основным компонентам. Содержание глинозема в них может составлять от 5 до 35%, редких элементов: Sr – 110 г/т, Zr – 2,30 г/т, Nb – 7 г/т, Ga – до 9 г/т и редкоземельных металлов: Y – 14 г/т, Eu – 0,68 г/т, La – 19 г/т, Pr – 7 г/т, Sm – до 15 г/т [4, 5]. Несмотря на низкое содержание РЗМ в золе, чем в известных их минералах (монацит: 264-280 г/т, лопарит: 112-180 г/т), при отсутствии разведанных источников, извлечение РЗМ из золы становится привлекательным и актуальным.
В Казахстане ежегодный выход золошлаковых отходов составляет около 19 млн. т. В золоотвалах к настоящему времени накоплено более 300 млн. т отходов. В одном только крупном мегаполисе Казахстана – в г. Алматы, в результате деятельности ТЭЦ-1, ТЭЦ-2 и ТЭЦ-3 накоплено более 2 млн. т золошлаковых отходов. Только за один отопительный сезон от сжигания угля, к накопленным объемам золы, добавляется около 600 тыс. т отходов золы. В Южно-Казахстанской области в результате деятельности Кентауской ТЭЦ образовано ряд полигонов золоотвалов, которые вывели из землепользования огромные площади и оказывают негативное воздействие на окружающую среду (загрязнение почвы, воздушного бассейна, грунтовых вод).
Актуальность и значимость работы усиливаются с фактом отсутствия рациональной технологии переработки золы. Многие ценные, технологически возвращаемые металлы безвозвратно теряются с золой. Золошлаковые отходы представляют собой сложную смесь, свойства которой зависят от вида угля и режима его сжигания, конструкции котла и многих других факторов. Это определяет необходимость проведения комплексных исследований состава и свойств минеральной части различных углей с целью использования их в качестве дополнительного источника для извлечения ценных металлов и получения товарных продуктов.
Значительные объемы накопленной золы ТЭЦ РК – дополнительный источник сырья для получения товарных продуктов с высокой добавленной стоимостью.
Технология переработки золы
По полученным ранее проведенных исследовании нами было построена технологическая схема комплексной переработки золошлаковых отходов ТЭЦ с получением чистого кремнезема и металлургического глинозема, представлена на рисунке 1.
Рисунок 1. Принципиальная технологическая схема комплексной переработки золошлаковых отходов ТЭЦ с получением товарных продуктов
Оптимальные технологические параметры и режимы процессов, составляющих основу технологии, представлены в сводной таблице 1.
Таблица 1.
Технологические параметры и режимы процессов
№№\пп |
Наименование процесса |
Параметры и режимы |
Значения |
1 |
Измельчение исходной золы |
Крупность |
100 меш |
2 |
Магнитная сепарация золы с получением товарного железосодержащего продукта |
Выход железосодержащего продукта / содержание железа / извлечение железа в товарный продукт, % |
10 / 50 / 80.
|
3
|
Обжиг немагнитной фракции золы совместно с хлоридом кальция в окислительной атмосфере |
Температура Продолжительность Расход CaCl2
|
1100 ºС 1 час 2 раза больше стехиометрии для разложения муллита |
4
|
Выщелачивание огарка соляной кислотой с получением товарного кремнезема |
Т:Ж Температура Продолжительность Концентрация HCl |
1:3 60 0 С 1 час 30 % |
5
|
Кристаллизация гексагидрата хлорида алюминия |
Температура Расход HCl-газа Концентрация HCl Продолжительность Промывка кристаллов |
60 оС 0,5 л/мин 26-30 % 1 час Многоразовая, HCl (30 %) |
6 |
Термическое разложение AlCl3·6H2O |
Температура Продолжительность |
450-500 оС 1 час |
7
|
Ректификация маточного раствора |
Расход NH4OH (25 %)
Температура Продолжительность |
Избыток 1,2 от стехиометрии для разложения хлоридов цветных металлов и РЗЭ 293 К 90 мин. |
Построенная технология была рассмотрена в двух аспектах: технологическая и эколого-экономическая.
Технологический аспект. Результаты процесса 2-х стадийного выщелачивания огарка соляной кислотой показывают, что построение технологии с целью ее оптимизации, в части сокращения расхода соляной кислоты и снижения объема раствора, не является однозначным. При 2-х стадийном выщелачивании, несмотря на двухкратное снижение объема раствора качество растворов, направляемых на дальнейший процесс кристаллизации гексагидрата хлорида алюминия, оставляет желать лучшего. Алюминий содержащие растворы характеризуются повышенным содержанием примесей, г/л: 69,05 Са: 0,46 Si; 1,81 Fe, что оказывает существенное влияние на извлечение кремнезема и качество получаемых продуктов в дальнейших процессах. Хотя во второй стадии и удается получение кремнезема высокого качества, % масс: Ca – 0,02; Al – 0,01; Fe – 0,02, циркуляция получаемого при этом промежуточного раствора состава, г/л: 5,86 Са; 1,86 Si; 1,89 Al; 0,07 Fe, ведет к потерям алюминия и кремния между продуктами. Как следствие, при организации процесса 2-х стадийного выщелачивания огарка не достигается высокого извлечения кремнезема в конечный товарный продукт. Извлечение кремния в товарный продукт составляет 98,1 %, против 99,7 %, соответствующей извлечению кремнезема в условиях одностадийного выщелачивания огарка соляной кислотой с 50-ти процентным ее избытком. Исходя из этого, применение одностадийного выщелачивания огарка представляется более перспективным. В пользу этого свидетельствует и то, что с практической точки зрения применение 2-х стадийного выщелачивания усложняет аппаратурно-технологическую схему общей технологии в целом. Выбор и использование 2-хстадийной технологии выщелачивания огарка должны осуществляться исходя из конкретных условий и возможности предприятий.
Эколого-экономический аспект. Ввиду отсутствия рациональной технологии переработки золы они не используются, а продолжают накапливаться, занимая большие территории и выводя их из землепользования. Использование разработанной технологии комплексной переработки золы позволит стимулировать развитие энергетической отрасли республики за счет повышения эффективности ТЭЦ путем вовлечения их в переработку в качестве дополнительного источника сырья с полной их утилизацией и получением товарных продуктов с высокой добавленной стоимостью. Исключение использования дорогостоящих материалов и реагентов, образования дополнительных твердых и/или жидких отходов, расширение ассортимента товарной продукции снизит издержки производства на ТЭЦ. Значительно уменьшаться объемы накопленной золы, сократятся энерго- и материальные затраты, расходуемые на складирование и хранение золы. Для эффективной глубокой очистки газов от SO2, NOx и CO2, получаемых при обжиге золы совместно с CaCl2, можно использовать технологии, описанные в работах [12, 13 7,8].
С экономической точки зрения применение новой технологии для комплексной переработки золы обеспечит стабильные условия для селективного извлечения ценных металлов в товарные продукты за счет использования новых технических решений («ноу-хау»). К примеру, по новой технологии при комплексной переработке 1 т золы (при усредненном ее составе) можно получить ~100 кг железосодержащего продукта, ~560 кг чистого SiO2 и около 265 кг металлургического глинозема (Al2O3) марки Г-0.
Исследования проводились в рамках грантового финансирования Комитета науки Министерство науки и высшего образования и Республики Казахстан на 2021-2023 годы по приоритетному направлению «Геология, добыча и переработка минерального и углеводородного сырья, новые материалы, технологии, безопасные изделия и конструкции» проекта № AP09259637 «Разработка высокоэффективной безотходной технологии для утилизации золы от сжигания угля с получением товарных продуктов».
Список литературы:
- Elliot Roth and other. Distributions and Extraction of Rare Earth Elements from Coal and Coal By-Products. 2017 World of Coal Ash Conference in Lexington, 2017, May 9-11.
- Aakash Dwivedi and Manish Kumar Jain. Fly ash – waste management and overview : A Review, Recent Research in Science and Technology 2014, 6(1): 30-35.
- Suhas V. Patil, Suryakant C. Nawle ,Sunil J. Kulkarni. Industrial Applications of Fly ash: A Review, International Journal of Science, Engineering and Technology Research (IJSETR), 2013, Volume 2, Issue 9, September, 1659-1663.
- Черкасова Т.Г. и др. Угольные отходы, как сырье для получения редких и рассеянных элементов. Вестник Кубанского государственного технического университета, 2016, 6, 185-18.
- Z.T. Yao and other. A comprehensive review on the applications of coal fly ash. Earth-Science Reviews 141 (2015) 105–121.
- Annalisa Zacco and other. Review of fly ash inertisation treatments and recycling Environ Chem Lett (2014) 12:153–175.
- Досмухамедов Н.К., Егизеков М.Г., Жолдасбай Е.Е. и др. Поведение NOХ при очистке отходящих газов ТЭС карбонатным расплавом щелочных металлов. Международный журнал прикладных и фундаментальных исследований. 2021. № 1. С. 30-34.
- Досмухамедов Н.К., Каплан В.А., Жолдасбай Е.Е. и др. Электрохимическое восстановление СО2 до СО в условиях электролиза карбоната лития при 900 ºС. Международный журнал прикладных и фундаментальных исследований. 2021. № 3. С. 59 -66