DEVELOPMENT OF DUAL COMPLETION DIRECTIONAL WELL DESIGN
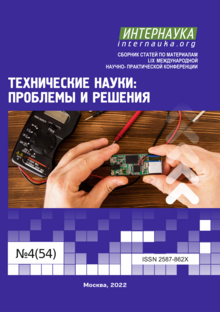
DEVELOPMENT OF DUAL COMPLETION DIRECTIONAL WELL DESIGN
Annaguly Deryaev
Candidate of Technical Sciences, Senior Researcher, Scientific Research Institute of Natural Gas of the State Concern "Turkmengas",
Ashgabat, Turkmenistan
ABSTRACT
The positive effect of the application of the dual completion technology (hereinafter “DC”) is the cut of capital investments for the construction of wells for each of the operational facilities, the reduction of operating costs and the development period of a multi-layer field, the increase in hydrocarbon production and the period of final oil recovery with profitable operation of wells.
Keywords: dual completion, well design, TBG, layout plan, drilling bit, casing column, slotted liner.
Nowadays abroad there is a significant increase in the introduction into the practice of oil and gas production of improved methods of field development with horizontal drainhole wells, as well as the use of the method of dual completion of wells.
Drilling wells with various wellbore deviations in new and old fields is carried out using devices for wellbore deviation and downhole telemetry systems for wellbore trajectory control with the appropriate software.
The interest of mining companies in drilling directional wells and dual completion wells is associated with the following factors:
- increase in flow rates in order to accelerate the development of the field without increasing the oil recovery factor;
- increase in flow rates without shortening the life of wells due to gas or water breakthrough through depression funnels;
- deconsolidation of the well placement grid at the new field and, accordingly, the number of required production wells;
- drilling directional wells from old wells in depleted fields to avoid grid compaction by new wells.
The dual completion program has strong support from manufacturing companies that produce devices for working in wells.
One of the most important tasks for successful drilling in areas with multi-layer productive horizons is the reasonable choice and development of dual completion wells design. The initial data for the engineering of well design are: purpose of drilling and purpose of the well, target horizon and well depth, diameter of the production casing column, formation pressures and hydraulic fracturing pressures of rocks of stratigraphic horizons, well completion and operation methods, well profile and its characteristics, characteristics of rocks by strength [1].
Data for the calculation (pressure and temperature by depth) of the investigated well №147 in the North Goturdepe area compiled on the basis of data from previously drilled wells №29, №97, №101, North Goturdepe.
Well design development starts with solving two problems: determination by calculation of the nominal diameters of the casing columns and the diameters of the rock destruction tool.
The number of casing columns is determined by a geological section analysis and well locations, presence of areas where drilling is associated with great complications, analysis of changes in reservoir anomalous pressure and absorption indices, as well as accumulated practical experience in well drilling.
The running depth of each casing column is specified in such a way that its lower end is in the interval of stable monolithic low-permeable rocks, and so that it completely covers the intervals of weak rocks, in which hydraulic fracturing can occur when opening zones of abnormally high formation pressure in the underlying interval [2].
Bit diameters, casing column diameters, transition depths from a larger diameter to a smaller one, casing column running depth, top of cement behind casing columns – all these constitute the concept of well design. The depth of the conductor descent is determined by the requirement of fixing the upper unstable deposits and isolating the upper aquifers or absorbing horizons.
While drilling oil and gas fields with high fractional pressure, it often becomes necessary to install preventers at the well-head of the conductor, then the installation depth of the conductor shoe is calculated from the condition of preventing hydraulic fracturing during the elimination of oil and gas manifestation according to formula (1).
(1)
The length of the conductor and the height of its cementing are chosen so that it is strong enough and can reliably withstand the forces that may occur when the preventer is closed under the pressure of productive formations. The possibility of gas breakthrough from the well along the annular space or along the fractures connecting the wellbore to the surface must also be excluded.
To select the number of intermediate technical columns and the depth of their descent, a combined diagram of changes in formation pressure, hydraulic fracturing pressure and hydrostatic pressure of the drilling mud column is built in the coordinates “depth – pressure gradient equivalent”.
The hydraulic fracture pressure is determined by formula (2).
(2)
In the rocks formation intervals, in which disturbance of the near-wellbore zone is possible, where the density of the drilling fluid is chosen taking into account rock pressure, the rock pressure is plotted on the combined diagram instead of fractional pressure.
The zones of compatible drilling conditions are the zones of well casing by casing columns, their number corresponds to the number of casing columns.
The compatibility of drilling conditions is meant a combination when the created parameters of the technological processes of drilling the underlying interval of the well will not cause complications in the drilled overlying interval, if the latter is not secured by the casing column.
The diameter of bits for drilling the selected casing column is determined by the required clearance between the column and the wellbore wall. The size of the clearance depends on the diameter and type of casing joints and the profile of the well, the complexity of the geological conditions, the hydrodynamic pressures during drilling and fixing the interval, and the exit from under the shoe of the previous column. The size of the clearance between the casing column and the wellbore wall is selected according to the analysis of the experience of drilling and casing wells in the given area and in similar geological conditions of other neighboring fields, or according to the results of specially designed research work made while drilling key boreholes in this area.
For the correct selection of the bottomhole design of directional and horizontal wells, it is necessary to study the lithological and physical characteristics of the deposits – reservoir properties of productive formations (porosity, permeability), mineralogy, thickness, conditions for their saturation with oil, physical and mechanical properties of rocks.
In order to conduct research within the framework of our scientific work and to select the dual completion directional well design of several productive formations in one well, a thorough study of previously drilled wells was carried out, and new types of well design were selected with a complete analysis of geological and geophysical materials.
Based on the parameters of fractional pressures at the corresponding depths, for well №147 we calculated the values of the equivalents of fractional pressure gradients using formula (3):
(3)
Based on the “Oil and gas industry safety rules” we find the value of the hydrostatic pressure of the drilling fluid in well №147.
According to formula 2, the values of hydraulic fracturing pressure and density of the drilling fluid for each well are determined separately.
After that, according to formula (4), the hydraulic fracturing coefficient was determined for each well under study separately.
(4)
On the well №147 of the North Goturdepe area, based on the combined pressure diagram and the calculation of the wellbore trajectory, the following design was chosen:
- mine direction Ø 720mm was set to a point of 10 meters, fixed with rubble concrete;
- extended direction Ø 630mm was set to a point of 30 meters in order to cover unstable, sandy-clayey deposits and prevent erosion of the wellhead when drilling under the surface conductor. Top of cement – up to the wellhead.
The surface conductor Ø426mm was set to a point of 596 meters, ensured the blocking of the upper part of unstable sandy-clayey quaternary deposits, isolation of the wellbore from waters hydrostatically connected with the surface and installation of blowout control equipment.
The technical casing column Ø324mm was set to a point of 2701 meters to block the swelling and caving formation of «blacktery», equipped with blowout control equipment and provides effective well control in case of possible manifestations. Top of cement behind the column – up to the wellhead.
The set of the technical column with a diameter of Ø244.5 mm was carried out to a point of 4206 meters (along the wellbore), (vertically) 4148 meters, into the roof part of the productive horizon IX d+e well log data guided. The shoe of the technical column was installed in clay deposits.
The casing column Ø244.5 mm was selected according to calculations to accommodate all the loads that occur during drilling and operation of wells. Top of cement behind the column – up to the wellhead.
The set of the production slotted liner – a filter Ø139.7mm, was carried out to a point of 4555 meters along the wellbore, (vertically) 4221 meters, with the installation of a liner hanger at 50-100 meters inside the casing column Ø244.5mm. The set of the slotted liner – a filter Ø139.7mm combined with casing pipes was carried out in order to mount the filter to the well wall and isolate productive formations from others. Mounting was carried out with special expansion packers installed as part of the lowered slotted liner – filter Ø139.7 mm.
When choosing and justifying the design of well No. 37 North Goturdepe, the requirements of the “Oil and gas industry safety rules”, the Regulations for calculating intermediate columns while drilling wells in the areas of the State Concern “Turkmennebit” were taken into account, and geological and technical information on previously drilled wells in the North Goturdepe area was used.
Based on the geological results and according to the calculations of the compatibility of drilling conditions due to the presence of four zones well casing, the structures of the investigated wells are represented by three casing columns, and the bottomhole part is a liner column.
A special difference of the design proposed by us for scientific testing from the previously used one is the increase in the depth of set of the second technical column Ø244.5mm for fixing the upper productive horizons, and the lower horizons with casing columns Ø139.7mm or special filters in the form of a liner.
The essence of this technology lies in the fact that set of two parallel TBG, which differ in suspension height – short and long – is available inside the production string (mainly Ø244.5 mm intermediate string). At the same time, productive horizons are separated by a packer device, which ensures their separate operation and accounting for well production for each production facility [3].
At the well №147 of North Goturdepe, for the purpose of dual completion of several productive horizons, the depth of descent Ø244.5 mm of the second technical column was increased to fix the upper productive horizons, and the lower horizons with special filters in the form of a liner without cementing.
References:
- Методические указания по выбору конструкций нефтяных и газовых скважин, проектируемых для бурения разведочных и эксплуатационных на площадях - Москва Миннефтепром, 1973.
- А.Г. Калинин. Бурение нефтяных и газовых скважин, - Москва ЦентрЛитНефтеГаз 2008.
- А.Р. Деряев. Разработка конструкции скважин для метода одновременно-раздельной эксплуатации нескольких нефтяных пластов. «Наука и техника в Туркменистане». №6. 2013. С 71-77.