ONE OF POSSIBLE APPROACH TO OBTAINING A ZINC FROM SECONDARY SOURCES BY THE ELECTROWINNING PROCESS
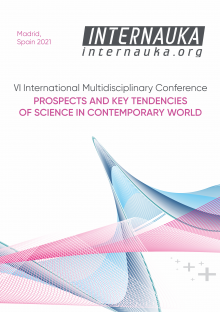
ONE OF POSSIBLE APPROACH TO OBTAINING A ZINC FROM SECONDARY SOURCES BY THE ELECTROWINNING PROCESS
Lyudmila Arkhipova
Postgraduate, NUST MISIS,
Russia, Moscow
Aleksandr Nikolaevich Fedorov
Assistant professor, Ph.D. of Engineering Sciences, NUST MISIS,
Russia, Moscow
ОДИН ИЗ ПОДХОДОВ К ПОЛУЧЕНИЮ ЦИНКА ИЗ ВТОРИЧНЫХ ИСТОЧНИКОВ ПОСРЕДСТВОМ ЭЛЕКТРОЭКСТРАКЦИИ
Архипова Людмила
аспирант, НИТУ «МИСиС»,
РФ, г. Москва
Федоров Александр Николаевич
доц., канд. техн. наук, НИТУ «МИСиС»,
РФ, г. Москва
Цинк является одним из наиболее широко применяемых цветных металлов, использование которого является гарантией устойчивого и долговременного развития общества. Цинк следует сложному жизненному циклу от добычи в составе руды, переработки и использования в обществе до возможного сбора и переработки его содержащих продуктов в конце срока службы. В процессе производства готовой продукции с использованием цинка и после вывода ее из потребления образуется большое количество отходов, содержащих данный металл [1].
Переработка техногенных отходов является серьезной проблемой современного мира как с экологической, так и экономической с точек зрения. Отвалы, созданные на протяжении десятилетий эксплуатации металлургических комплексов, оказывают неослабевающий негативный эффект на почвенный покров местности, гидро– и атмосферу, а через них на состояние фауны, флоры и здоровье человека. Главными компонентами, отрицательно влияющими на экологию территорий складирования и захоронения, являются тяжелые цветные металлы и их соединения, не последнее место среди которых занимает цинк в виде различных соединений.
Основное количество шламовых отходов современного производства по содержанию железа удовлетворяет требованиям последующей утилизации в металлургическом переделе, но высокое содержание примесей – цинка и свинца, является основным препятствием при рециклинге шламов и пылей металлургических предприятий. В результате на ряде металлургических заводов приняты решения об уменьшении или полном выводе пылей и шламов текущего производства из оборотного цикла, что приводит к ежегодным потерям миллионов тонн железа и сотен тысяч тонн цинка.
В последние годы в связи с необходимостью решения экологических задач и имеющим место снижением содержания ценных компонентов в рудах повышается значение комплексного использования добываемого сырья и сокращения промышленных отходов и выбросов, представляющих возможный дополнительный источник сырья для цветной и черной металлургии.
Ежегодно предприятия черной металлургии отправляют на временное хранение в отвалы пыли с повышенным содержанием цинка в количестве
5–10 % от массы выпущенного товарного металла. Суммарный мировой прирост цинксодержащей пыли оценивается в 10–15 млн. тонн в год. Существуют также отдельные техногенные месторождения с содержанием цинка, достигающим 30 %, среднее же содержание по цинку оценивается в 8–10 %. Кроме того, в пылях содержится 30–60 % оксидов железа и до 20 % оксидов кремния, кальция и свинца (суммарно).
Ужесточение природоохранных требований, сделало захоронение пылей дорогостоящим вариантом, а прямая утилизационная переработка на железосодержащую продукцию ограничена из–за накопления в них тяжелых цветных металлов.
Разработка и внедрение новых передовых технологий, позволяющих извлекать из шламов и пылей технологически опасные компоненты и тем самым осуществлять регенерацию железосодержащих отходов до сырьевого состояния для повторного вовлечения в производство, выходит на первый план.
На текущий момент годовое производство стали в России составляет примерно 70 млн. тонн [2], из которых основное количество приходится на дуговые сталеплавильные печи (ДСП).
Пыль ДСП по физическим свойствам, химическому и вещественному составам очень сложный, неоднородный материал, трудно поддающийся системной классификации. Химический состав пылей колеблется значительно и зависит от вида и состава используемого сырья (лома) и шихтовых добавок, технологии плавки, типа и марки выплавляемой стали. Также степень возврата пыли в процесс влияет на химический состав образующейся пыли. Кроме того, даже небольшие корректировки в технологии между плавками могут приводить к изменению состава пыли, для чего необходимо проведение полного анализа продуктов каждой плавки в целях оптимизации любой рециркуляции.
Важнейшим элементом пылей является железо, содержание которого варьируется от 16 до 44 %, а средняя концентрация его составляет около 30 %. Соединения цинка являются основными сопутствующими компонентами в пыли, и их концентрация может изменяться в интервале 2 – 40 %. Кроме того, пыль ДСП содержит небольшие количества свинца, марганца, кальция, натрия и калия, а также следы других элементов, таких как кадмий, хром, никель, медь, магний, кремний и хлор.
По вещественному (фазовому) составу пыль ДСП – это смесь оксидов металлов, силикатов и сульфатов. Формы нахождения цинка в пыли крайне важны при выборе способа его извлечения. Цинк преимущественно присутствует в виде двух основных соединений – цинкита (ZnO) и феррита цинка (ZnFe2O4) [3]. Отношение этих фаз зависит от типа печи, технологических операций плавки и особенно от применяемой системы газоочистки. Доля цинка в виде цинкита может варьироваться от 30 до 70 %.
Для комплексной утилизационной обработки вторичных материалов, включая цинксодержащие шламы и пыли, могут быть использованы пирометаллургические или гидрометаллургические процессы (способы), или их разнообразные сочетания. Ввиду мало–масштабности, территориальной разобщенности, сложности и разнообразия химического и вещественного состава отходов предпочтение отдается гидрометаллургическим процессам, которые, как показывает практика заводов цветной металлургии, являются более экологически безопасными и экономически эффективными для переработки сырьевых материалов различного происхождения с относительно невысоким содержанием цинка.
Гидрометаллургические способы переработки цинксодержащих отходов делятся (и, соответственно, именуются) по типу основного или головного процесса – выщелачивания: сернокислотное [4–5], солянокислое [6–7], уксусная кислота [8–9], щелочное [10–11], карбонат–аммиачное [12] и др. В недавнем прошлом большое количество исследований было сосредоточено на разработке щелочного метода извлечения цинка из пылей ДСП, основанием которых послужила высокая избирательная способность щелочи (например, едкого натра) к переводу цинка в водный щелочной раствор при практически индифферентном отношении к металлам подгруппы железа. Обнадеживающие результаты применения щелочного выщелачивания цинксодержащих пылей и шламов [11, 13-19] являются достаточным основанием для разработки последующего электро–гидрометаллургического процесса получения металлического цинка электролизом цинкатного водного раствора.
Электролиз – завершающий, но не конечный этап гидрометаллургического производства цинка. Показатели электролиза во многом зависят от качества выполнения предшествующих операций: выщелачивания, очистки растворов от примесей. Около 80 % цинка получают в процессе электролиза как из первичных, так и из вторичных сырьевых источников [20].
Очевидными преимуществами электролиза щелочных цинкатных растворов являются высокая чистота получаемого металла, применение традиционных («некислотостойких») конструкционных материалов.
Как показывает литературный обзор, большое количество исследований по рассматриваемой тематике электролиза цинкатных растворов [17-18, 21-23] носит разрозненный, несистемный характер, и направлено, в своем большинстве, на решение конкретной утилитарной задачи – получение цинковых порошков. Авторами проведены как лабораторные, так и полупромышленные исследования, рассмотрены влияния состава электролита (концентрации щелочи и цинка), температуры, плотности тока в достаточно широком интервале изменения их значений, применены различные материалы для изготовления катодов и анодов. Тем не менее, к настоящему времени не найдено исчерпывающего теоретического объяснения механизма образования порошков при электроосаждении цинка из щелочных растворов. Надо также отметить, что не все разработки дошли до коммерциализации, имеется информация только о небольших фабриках в Китае [24].
В то же время, из доступных данных [18, 21, 24] не следует единого мнения об условиях и параметрах промышленной реализации процесса щелочного электролиза.
Основываясь на научно–теоретических представлениях об организации и последующей надежной, эффективной и безопасной эксплуатации современного металлургического производства, можно однозначно констатировать, что общая технологическая схема переработки цинксодержащего сырья определяется (или подчинена) конечной стадией производства товарного металла.
Используя профессиональный подход к разработке новой технологии для решения проблемы переработки цинксодержащих отходов производства стали в части электроэкстракции цинка из щелочных растворов, необходимо решить три первостепенные задачи:
– создать теоретический базис – электрохимические основы извлечения цинка из щелочных растворов с определением соответствующих условий и параметров для их промышленной реализации;
– разработать принципиальные конструктивные решения по аппаратурному оформлению цинкат–щелочного электролиза (основное технологическое оборудование – электролизер);
– концептуально проработать аппаратурно–технологическую схему, принципы и порядок ее функционирования как производственного подразделения.
Выявление в ходе выполнения отмеченных выше задач недостающих технических данных и технологических параметров необходимо для организации технологии процесса электролиза промышленного масштаба, что является завершающим этапом в цепочке переработки шламов и пылей ДСП не только текущих объемов, но и накопленных в промышленных зонах отвалов на территории Российской Федерации.
Список литературы:
- Zinc international association. Material Stewardship. – URL: https://sustainability.zinc.org/stewardship/ (дата обращения 20.03.2021).
- Cборники конференций ИНТЕХЭКО / ООО «ИНТЕХЭКО» – инновационные технологии и экология. – URL: http://www.intecheco.ru/doc/sb_met2014.pdf (дата обращения 20.03.2021).
- Lenz D.M., Martins F.B. Lead and zinc selective precipitation from leach electric arc furnace dust solutions // Revista Matéria. – 2007. – № 12.
- Oustadakis P., Tsakiridis P.E., Katsiapi A., Agatzini–Leonardou S. Hydrometallurgical process for zinc recovery from electric arc furnace dust (EAFD): Part I: Characterization and leaching by diluted sulphuric acid // Journal of hazardous materials. – 2010. – V.179. – № 1.
- Trung Z.H., Kukurugya F., Takacova Z., Orac D., Laubertova M., Miskufova A., Havlik T. Acidic leaching both of zinc and iron from basic oxygen furnace sludge // Journal of Hazardous Materials. – 2011. – V. 192. – № 3.
- Sarka L., Juraj L., Dalibor M. Selective leaching of zinc from zinc ferrite with hydrochloric acid // Hydrometallurgy. – 2009. – V. 95. – № 3.
- Vazarlis H.G. Hydrochloric acid–hydrogen peroxide leaching and metal recovery from a Greek zinc–lead bulk sulphide concentrate // Hydrometallurgy.
– 1987. – V. 19. – № 2. - Dreissinger D.B., Peters E. Morgan G. The hydrometallurgical treatment of carbon steel electric arc dust by the UBC – Chaparral process // Hydrometallurgy.
– 1990. – № 25. - Barrett E.C., Nennigera E.H., Dziewinskib J. Hydrometallurgical Process to Treat Carbon Steel Electric Arc Furnace Dust // Hydrometallurgy. – 1992. – V. 30.
– № 1–3. - Zhang C., Zhuang L., Wang J. Extraction of zinc from zinc ferrites by alkaline leaching: enhancing recovery by mechanochemical reduction with metallic iron // The Journal of the Southern African Institute of Mining and Metallurgy. – 2016. – V. 116.
- Orhan G. Leaching and cementation of heavy metals from electric arc furnace dust in alkaline medium // Hydrometallurgy. – 2005. – № 78.
- Nyirenda R. L., Lugtmeijer A. D. Ammonium carbonate leaching of carbon steelmaking dust. detoxification potential and economic feasibility of a conceptual process // Minerals Engineering. – 1993. – № 6.
- Li H.–X., Wang Y., Cang D.–Q. Zinc leaching from electric arc furnace dust in alkaline medium // Central South University Press and Springer–Verlag Berlin Heidelberg. – 2010.
- Stefanova A., Aaroma J., Forsen O. Alkaline leaching of zinc from argon oxygen decarbonization dust from stainless steel production // Physicochemical Problems of Mineral Processing. – 2012. – № 49.
- Dutra A.J.B., Paiva P.R.P., Tavares L.M. Alkaline leaching of zinc from electric arc furnace steel dust // Minerals Engineering. – 2006. – № 19.
- Stefanova A., Aaroma J. Alkaline leaching of iron and steelmaking dust // School of Chemical Technology. – 2012. – V.1.
- Youcai Z., Stanforth R. Integrated hydrometallurgical process for production of zinc from electric arc furnace dust in alkaline medium // Journal of Hazardous Materials. – 2000. – № B80.
- Jiachao J., Xiaoyu Y., Youcai Z. Recovery of zinc from EAF dust by alkaline extraction // Advanced Materials Research. – 2010. – V. 113–116.
- Ashtari P., Pourghahramani P. Zinc Extraction from Zinc Plants Residue Using Selective Alkaline Leaching and Electrowinning // Journal of the Institute of Engineering. – 2015. – № 96 (2).
- Jha M.K., Kumar V., Singh R.J. Review of hydrometallurgical recovery of zinc from industrial wastes // Resources, conservation and recycling. – 2001. – V. 33 (1). – № 1.
- St–Pierre J., Piron D.L. Electrowinning of zinc from alkaline solutions // Journal of applied electrochemistry. – 1986. – № 16.
- Li Q., Zhao Y., Jiang J., Zhang C. Optimized hydrometallurgical route to produce ultrafine zinc powder from industrial wastes in alkaline medium // Procedia Environmental Sciences. – 2012. – № 16.
- Zhao Y., Li Q., Zhang C., Jiang J. Production of ultrafine zinc powder from wastes containing zinc by electrowinning in alkaline solution // Brazilian Journal of Chemical Engineering. – 2013. – № 4.
- Jiang J., Zhao Y., Guo C. Production of zinc powder by alkaline hydrometallurgy // Applied Mechanics and Materials. – 2010. – V. 26–28.