THE INFLUENCE INITIAL IRON POWDER PARTICLES PROPERTIES ON THE Fe-Cu-Sn-Ni COMPOSITION PRESSING SINTERING KINETICS
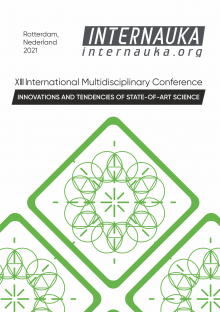
THE INFLUENCE INITIAL IRON POWDER PARTICLES PROPERTIES ON THE Fe-Cu-Sn-Ni COMPOSITION PRESSING SINTERING KINETICS
Nikoloz Loladze
PhD, Professor, Georgian Technical University,
Georgia, Tbilisi
Medea Tserodze
PhD, Associate Professor, Georgian Technical University,
Georgia, Tbilisi
Zurab Avalishvili
PhD, Assistant Professor, Georgian Technical University,
Georgia, Tbilisi
Iuri Dzidzishvili
Master, Georgian Technical University,
Georgia, Tbilisi
The work has been carried out under the grant of Shota Rustaveli National Science Foundation of Georgia (Contract AR – 18 – 1911)
Keywords: Powder dispersion, morphology, sintering process.
Background
Powder metallurgy is one of the progressive processes for obtaining products for various purposes. Numerous powder metallurgy processes give opportunity to reduce material consumption and energy expenses. Powder metallurgy is technology that uses metallic powders (or mixtures of metallic and non-metallic powders) as a raw materials to produce metallic materials, composites and various types of products after forming and sintering. Due to the advantages of powder metallurgy technology, it has become the key to solving new material problems and play a key role in the development of new materials.
Powder commonly used in powder metallurgy are characterized by again particle size distribution. The manufacturing process of a sample by powder metallurgy is conditioned by the properties of initial powders [1]. One of the most relevant properties is particle size distribution. Properties such as apparent density, flowability, specific area and compressibility depend on particle size distribution [2]. Results show that the size and shape of particles has significant influence on the sintering process.
Porosity is inversely proportional to sintered material density and depends on the size and shape of particles as well as applied compacting pressure (among others). Furthermore, the particle size influences the sintering process itself in addition to the properties of readymade parts.
Powders of small average particle diameter are used when high mechanical properties desired. It has been reported that small particles generate a lot of inter particle frictions. This restrikes the powder flow rate. In the compaction process the use of small metallic particles originates problems during pressing step [3].
On the other hand, powder of large size is used to enhance mixing and compacting process. The mechanical properties of sintered samples do not depend only upon particle size distribution. Morphology structure and micro porosity are also important. It has been reported models which describe powder behavior during the compaction process of irregular and spherical powder [4].
The use of small particle size is based in the improvement of the mechanical properties of the sintered sample. Higher surface area increases number of bonds among the particles. Then, a more efficient solid-state diffusion process is obtained due to the proximity of powder particles.
To intensify the sintering process, in most cases, the so-called activated sintering method is used. Activated sintering is the sintering process of powder forming under the influence of chemical and physical factors.
Physical methods of activated sintering are associated primarily with an increase in the dispersion of the powder and the defect in the crystal lattice of the substance. Intensive grinding of particles increases their total surface, increasing the reserve of excess energy of the powder and increases the "thickness of the damaged layer". This promotes the action of such a mass transfer mechanism as "surface diffusion". Grinding is understood as a change in the initial particle size of the material by breaking them down under the action of external forces that overcome the internal molecular forces. During the grinding, crushing and impact processes are combined. When crushing solids, the expended energy is spent on elastic and plastic deformation, on heat and the formation of new surfaces, which is the final goal of their transformation into powder.
It is known that dispersed powders have high sintering activity [5, 6]. During joining dispersed particles, the driving force of the process is the thermodynamic potential gradient caused by the concentration gradient of vacancies arising on curved surfaces. The density of defects in the crystal structure and the curvature of the surface of the powders can be significantly changed during grinding of the powders and thereby activate sintering. By changing the parameters of the grinding process, it is possible, at a certain level, to regulate the fineness and morphology of the particles of the final product. Knowledge of the regularities of the behavior of metal powders with different particle size distribution and morphology in the sintering process is very important when developing new cost-effective technologies for the production of new functional materials.
The main objective of the work was to determine the influence of particle size distribution and morphology on sinterability and the kinetics of multicomponent powder compositions sintering process.
For this purpose, Fe -Cu -Sn -Ni (47 -32 -8 -13) composition was used given composition is well-known and reviewed in the scientific literature and widely used for the production of diamond tools.
Methods
Powders of iron “PJI M2”, copper “MPS-1(Cu – 99.5%), nickel “PNE1”, Tin “PO-1” (metals powders grade in Russian), were used starting materials for the manufacture of metal compositions for sintering. Content of impurities in metal powders no more that 0.5% mass.
Iron powder with an initial grain size of 200/100 µm was subjected to mechanical treatment. The iron coarse powders were bill milled in ceramic ball mill in ethanol medium. The weight ratio of “balls” to powder was 1:6. The powders were ball milled for 10, 20 , 30, 50 and 80 hours at 60% critical speed. After milling the powders were dried in oven at 600C for 10h. After milling the powders were tested for particle size and shape. Subsequently, particle size was measured using Laser Diffraction Particle Size Analyzer (Malvern Panalytical Mastersizer 2000, Japan). The microstructure and morphology of the powder were observed by scanning electron microscopy (SEM microscope TM3030Plus, Hitachi).
Mixtures of metal powders for sintering were prepared by mixing needed powders during 60min. in industrial mixer. The dispersion and morphology of the main component, Fe, were changed. The -63µm fraction (after saving) of the original iron powder (water atomized) was used as well as activated by ball milling for 50 and 80h initial powder of grain size 200/100µm. The obtained iron powder of various grain size and morphology was used for sintering. The granulate of the rest of the powders (Cu, Sn, Ni) used in the sintering process had the some granulate of <50µm.
The sintering process was performed in cylindrical molds by hot pressing. The developed sample (sinters) was about 15mm in diameter and 9 mm in height. Graphite CPV 14814000 was used as hot pressing molds material. The process was conducted in conditions of pressure - 40 MPa, the sintering temperature 780 - 8000C and the holding time at the sintering temperature 15sec., 60sec. and 120sec.
Density calculation of sintered composites were performed by formula:
Y = m1 · y water / m1 – m2
Where m1 - the mass of the sample in air, g;
m2 - the mass of the sample in water, g;
y - the density of water at the measurement temperature, g/cm3.
The mass was measured with an accuracy of 10-4g.
Also, the hardness of sintered samples was characterized by the Rockwell B scale.
Results and Conclusions
As was noted above for revealing the difference and to establish the role of the initial powder dispersion and morphology on the kinetics of the sintering process under hot pressing conditions a series of experiments was carried out.
Iron powder characteristics “before and after” ball milling for 50 and 80h, size distribution, mean particle size, specific surface area and morphology structure are presented in table 1.
Table 1.
Milling time and physical characteristics of iron powders
## |
Initial Size µkm |
Milling Time h |
Average Mass diameter µm |
Min and max diameters µm |
Spetsific surface area m2/gr |
Morf. structure |
|
200/100 |
0 |
|
|
|
|
1 |
-63 |
0 |
43 |
20 - 82 |
0.287 |
|
2 |
200/100 |
50 |
68 |
21 - 130 |
0.226 |
|
3 |
200/100 |
80 |
30.4 |
69 - 75 |
0.457 |
|
It was found that as the grinding time increases the shape of the initial particles of iron powder changes and from spheroidal becomes more and more flat and flaky. Study after mechanical activation of iron powders showed, that during milling the iron powder particles are repeatedly flattened, work-hardened fractured and sometimes welded together. After 50 hours and especially 80 hours of milling they show flaky shape (table 1, sample 2, 3).
The effect of starting powder particle size on pressure sintering kinetics of Fe -Cu -Sn -Ni alloys was investigated.
The study of the kinetics of the sintering process will provide an opportunity for a better understanding of the mechanism of consolidation of the powder mass under conditions of high P and T. The sinters’ values of density and hardness dependence on the duration of exposure at operating temperatures were studied. Knowing the density and hardness values of the samples in the entire volume gives practically the maximal vision of the sinter ability of the powders and the completion of the consolidation process at specific sintering parameters.
Image 1. a, b, c, demonstrate kinetic curves of density and hardness of sintered specimens, when the initial charge contains iron powder: water atomized fraction -63μm (a), iron powder ball milled for 50h(b), and ball milled during 80h(c).
a
b
c
Figure1. Kinetic curves of density and hardness of sintered specimens, water atomized fraction -63μm (a), iron powder ball milled for 50h(b), ball milled during 80h(c)
The effect of water atomized iron powder grinding time variation (from 0 to 80h) on the powder particle size distribution was studied (Table 1). Experimental data show that with an increase in the milling time, the average size of the conglomerates decreases; this is most clearly demonstrated after 50 hours of milling. A slight increase in particles average size at a grinding time from 0 to 50 hours [7] may be due to the appearance of micro-sized particles with tendency to agglomeration. A significant decrease in size after 50 h of grinding can be associated with the accumulation of defects in the crystal structure and destruction of particles.
Figure 1 shows the changes in the density and hardness of sintered samples of the Fe –Cu –Sn –Ni system depending on the duration at the max. sintering temperature, when iron powder is ball milled 0 hours a) ball milled 50h. b) ball milled 80 hours. A change in the physical characteristics of the sinters was observed at different durations of the sintering process. The physical parameters of the sintered specimens — density and hardness — were defined, since they give a sufficient picture of the process nature. The values of the density (porosity) of the samples indicate the degree of consolidation caused by the viscous flow of metals, while the homogeneity and change in the sample hardness indicates mostly the phase formation process running.
The data presented on the kinetic curves show, that the maximum density is achieved, when untreated water atomized initial iron powder is used (dispersion -63 µm) with a nearly spherical shape. This could be explained by a geometric factor - large spherical particles give few pores when packed. At the same time, the hardness of the samples is minimal and practically does not change according to a duration of process. This indicates a low intensity of diffusion processes responsible for the formation of new phases - solid solutions and intermetallic compounds with a higher value in hardness.
Activation of iron powder practically does not affect sintered compositions density (Fig. 1 b, c). To some extent, as the specific surface area increase and change morphology changes, the compaction process becomes more problematic, that agrees with the data of work [1]. The activation of the iron powder significantly changes the samples hardness – as the duration of grinding increases, the surface area increases as well, i.e. contact surface of powder particles. Most likely, the increase in the hardness of the samples (Fig. 1, c) is associated more with a greater extent with the intensification of the phase formation process than with the compaction process.
In addition to increasing the specific surface area and the contact surface, crystal lattice defects formed during powder grinding affect the diffusion processes rate. In accordance with the vacancy theory of diffusion [8], the diffusion coefficient is proportional to the vacancy concentration.
The data obtained are in good agreement with the data of various authors and do not contradict the general laws of dispersed systems sintering theory.
References:
- F.Sanchez, A.M.Bolarin, P.Molera, J.E.Mendoza and M.Ocampo. Ralationship between particle size and manufacturing processing and sintered characteristics of iron powders. Rev. Latin Am. Met. Mat. v. 23 n.1 Caracas, pp.35-40, 2003.
- J. E. Peterson and W. M. Small "Physical behavior of water-atomized iron powders: Particle size distribution and apparent density Mechanical Behavior of Material ", The International Journal of Powder Metallurgy , Vol 29, No. 2, pag 131-137, 1993.
- D. Poquillón, J. Lemaitre et al. Cold Compaction of Iron Powders-relations between Powder morphology and mechanical properties. Part I: powder preparation and compaction. Powder Technology, 126, pp. 65-74, 2002.
- D. Poquillón, J. Lemaitre et al. Cold Compaction of Iron Powders-relations between Powder morphology and mechanical properties. Part II: Bending Test: results and analysis. Powder Technology, 126, pp. 75-84, 2002.
- S.A.Oglazneva, M.N.Portalov. Study of kinetics of isothermal sintering grinded and mechanically alloyed iron powders. Theory and processes of molding and sintering of powder materials. #1, pp.9-16, 2014. (In Russian).
- S. V. Matrenin, et al. Activating the sintering process of iron powders by introducing Nano dispersed additives. Izv. Universities. Powder metallurgy and functional coatings. no. 2. pp. 11-16, 2009. (In Russian).
- N.Loladze, M.Tserodze, Z.Avalishvili, i.Dzidzishvili. The effect of particle size and morphology on the sinter ability of Fe-Cu-Sn-Ni composites. Recent scientific Investigation Proceedings of XXIV International Multidisciplinary Conference, Shawnee, USA, pp.27-35, Seftember, 2021.
- L.N. Dyachova.Features of formation of the structure and properties of powder steels with additive diffusion processes during sintering. Proceeding of National Academy of Sciences of Belarus. Physical-technical series, v.65, no.1, pp.43-53, 2020. (In Russian).