THE MACROSCOPIC MORPHOLOGY OF WIRE ARC ADDITIVE MANUFACTURED AL-5MG ALLOYS
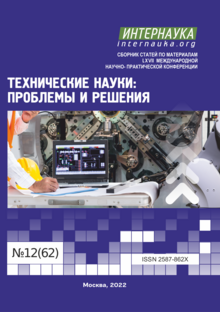
THE MACROSCOPIC MORPHOLOGY OF WIRE ARC ADDITIVE MANUFACTURED AL-5MG ALLOYS
Chuanc Su
Student, Samara National Research University, Samara,
Russia, Samara
Lei Huang
Student, Samara National Research University,
Russia, Samara
Sergey Konovalov
Professor, Siberian State Industrial University,
Russia, Novokuznetsk
ABSTRACT
The Al-5Mg alloys are fabricated by wire arc additive manufacture based cold metal transfer technology (WAAM-CMT) using three different arc modes (CMT, CMT+A, CMT+P) to study the macroscopic morphology of the Al-5Mg samples. The results show that the forming surface of the Al-5Mg samples in the CMT arc mode is the flattest and the most uniform, and the forming is best. Compared with the CMT+P modes, the effective width (Weffective) and effective utilization rate (Seffective) of the cross-section of the Al-5Mg sample in the CMT+A and CMT arc mode are the higher, which are 13.51mm/0.87 and 11.53 mm/0.85 respectively. Among the samples, the Seffective has a small change, and its values are all above 0.81, which presents the material utilization rate of the WAAM-CMT technology is higher.
Keywords: WAAM-CMT, arc mode, effective width, effective utilization rate.
1. Introduction
During the WAAM process, the forming quality of the material is largely affected by the metal transfer process. During this process, the fuse is guided to the molten pool by an arc created between the wire and the substrate [1-3]. At present, three main metal transfer methods include: spray transfer, ball transfer, and short-circuit transfer, which are mainly controlled by welding sources using high-frequency control strategies. The CMT technology developed by Fronius' company is an improved GMAW process and is a more suitable manufacturing process for aluminum alloys WAAM, CMT or cold arc mode reduces the overall heat during deposition compared to traditional GMAW mode of operation input, using cold arc mode instead of the self-regulating GMAW process reduces heat input by 16% [4-6]. The reduction in heat input increases deposition efficiency at lower penetration depths. In this study, the ER5356 wire was adopted as raw material to fabricate Al-5Mg alloys by using WAAM-CMT technology. And the macroscopic morphology of the Al-5Mg sample at different arc modes were studied.
2. Materials and methods
In the experiment, the Al-5Mg alloys with a dimension of 150 mm × 8 mm × 70 mm were deposited by WAAM-CMT system under CMT, CMT-P, CMT-ADV arc mode, respectively. And the parameter settings are as follows: ER5356 (Al-5Mg) alloy filler wire (FW) with a diameter of 1.2 mm was selected as the deposition material. The wire feed speed, deposition speed and Ar flow rate were set as 5.5m/min, 0.6m/min and 25L/min, respectively. Before processing, the 6061-T6 aluminum alloy plate with the size of 200mm × 60mm × 10mm was mechanically cleaned and fixed on the workbench as the base metal (BM). The nominal chemical composition of BM and FW is listed in Table 1. And the effective utilization rate (S) was calculated using Eq. (1):
S= Seffective / Sall (1)
Seffective and Sall were effective area and all area for each sample.
Figure 1. (a) The WAAM-CMT system; (b) Weffective: effective width, mm; (c) Seffective: effective area, mm2
Table .1
Chemical composition of 6061-T6 aluminum alloy and ER5356 wire (wt%)
3. Results and discussions
The macro topography and cross-sectional appearance of the WAAM-CMT thin-walled samples are shown in the Fig.1. Since the thin-walled sample is fabricated in a multi-layer and multi-channel method, the surface of the sample is corrugated, and its amplitude is directly related to the utilization rate of the material. Under the condition of different heat input, the forming flatness of the forming sample surface (that is, the fluctuation of the overall sample forming surface) decreases with the increase of heat input, and the perpendicularity of the cross-section of the sample (that is, the inclination of the two side walls of the sample forming section) is also reduced. For the WAAM-CMT, the technology has multiple arc modes, including CMT+P, CMT, CMT+A mode, and the heat input of different modes is obviously different. The relationship of the heat input of the arc mode is: CMT+P > CMT > CMT+A. Comparing the forming conditions of the Al-5Mg samples prepared in each mode, it can be seen that the forming surface of the Al-5Mg samples in the CMT arc mode is the flattest and the most uniform, and the forming is best. However, for the corrugated surface of the Al-5Mg sample formed in the CMT+P arc mode, the amplitude difference between the layers is too larger, and the flatness is poorer. The effective width and effective utilization of the sample formed cross-section are shown in Table.2. Compared with the CMT+P modes, the Weffective and Seffective of the Al-5Mg sample in the CMT+A and CMT arc mode are the higher, which are 13.51mm/0.87 and 11.53 mm/0.85 respectively. The Weffective and Seffective of the Al-5Mg sample in the CMT+P arc mode are the lowest, which are 14.17 mm/0.81 respectively.
Figure 2. The macroscopic morphology of Al-5Mg alloys at different arc mode (cross sectional appearance): (a) CMT+A; (b) CMT; (c) CMT+P
Table 2.
The geometrical dimensions of Al-5Mg alloys at different arc mode
Sample |
Effective utilization [%] |
Effective width [mm] |
Effective area [mm2] |
CMT+A |
0.87 |
13.51 |
788.98 |
CMT |
0.85 |
11.53 |
723.85 |
CMT+P |
0.81 |
14.17 |
793.23 |
4. Conclusions
The effective wall width (Weffective) is dependent upon variation in arc mode, which presents a highest in CMT+P mode, whose value is 13.4 mm. And the arc mode directly affects the availability of the material, among the samples, the Seffective has a small change, and its values are all above 0.81.
References:
- Kawalkar, R. Wire arc additive manufacturing: A brief review on advancements in addressing industrial challenges incurred with processing metallic alloys [Text] / R. Kawalkar, H. K. Dubey, S. P. Lokhande // Materials Today: Proceedings. – 2021.
- Vafadar, A. Advances in metal additive manufacturing: a review of common processes, industrial applications, and current challenges [Text] / A. Vafadar, F. Guzzomi, A. Rassau, K. Hayward // Applied Sciences. – 2021. – Vol. 11 (3). – P. 1213.
- Sun, J. Wire–powder–arc additive manufacturing: A viable strategy to fabricate carbide ceramic/aluminum alloy multi-material structures [Text] / J. Sun, H. Yu, D. Zeng, P. Shen // Additive Manufacturing. – 2022. – Vol. 51. – P. 102637.
- Selvi, S. Cold metal transfer (CMT) technology-An overview [Text] / S. Selvi, A. Vishvaksenan, E. Rajasekar // Defence technology. – 2018. – Vol. 14 (1). – P. 28-44.
- Cornacchia, G. Study and Characterization of EN AW 6181/6082-T6 and EN AC 42100-T6 Aluminum Alloy Welding of Structural Applications: Metal Inert Gas (MIG), Cold Metal Transfer (CMT), and Fiber Laser-MIG Hybrid Comparison [Text] / G. Cornacchia, S. Cecchel // Metals. – 2020. – Vol. 10 (4). – P. 441.
- Mezrag, B. Indirect approaches for estimating the efficiency of the cold metal transfer welding process. [Text] / B. Mezrag, F. Deschaux Beaume, S. Rouquette, M. Benachour // Science and Technology of Welding and Joining. – 2018. – Vol. 23 (6). – P. 508-519.